1. Making Patterns Resin or
aluminum patterns will be necessary for green sand
casting process. Without patterns, the production
for castings will be impossible. Sometimes, wooden
patterns could be used for small quantity
production, but for batch production, resin or
aluminum patterns will be needed.
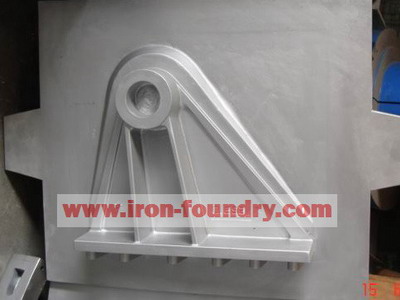
2. Molding Process
There are three types of molding
methods by green sand, one is manual molding, second
is by molding machine, third is by automatic molding
equipment.
The following is manual molding
workshop, which is very traditional molding method,
but it is still existed because of its advantages,
because it can produce large castings.
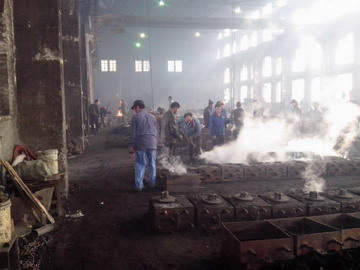
The following is showing the molding machine, which
could save manpower, and produce better quality
castings, however, because of the size limitation of
sand boxes, it can not produce large castings.
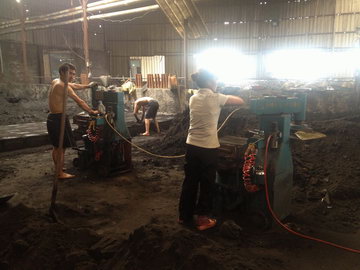
3. Iron Melting and Pouring
Melting could be done by the cupola (coal as the
fuel), or medium frequency electrical furnaces. Both
furnaces could meet the material requirements as
long as the foundry could handle their operation.
Comparatively, the electrical furnaces could keep
the quality better and more stable.
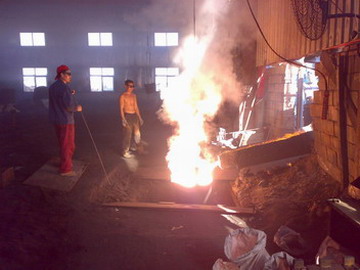
4. Sand Blasting and Grinding
After the iron castings taken out
from sand molds, they will be put into sand blasting
equipments to remove sands, then the workers will
grind the gating heads, parting lines and sharp
edges. Then, the rough castings will be completed.
If the castings need further
machining and painting, then they will be taken to
machining workshop or painting workshop.
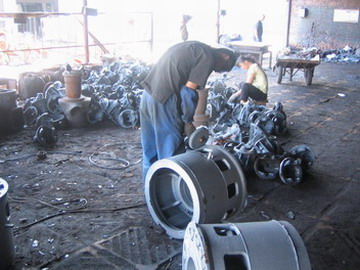
|