1. Making Pattern Patterns
are necessary tooling for making castings. All
wooden patterns, resin (plastic) patterns and
aluminum patterns could be used to produce resin
sand castings. Aluminum patterns will be the most
expensive ones, but they could be used to produce
thousands of castings, and can guarantee higher
dimensional tolerance and better surface quality.
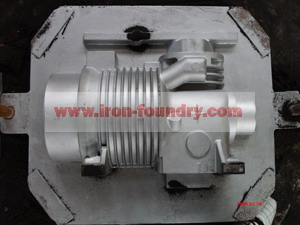
2. Molding Process
The resin sand will be mixed by
the sand treatment equipment, then shoot into the
sand boxes (flasks). The molding workers will
guarantee the sand can be filled to all positions,
and make the sand as solid as possible.
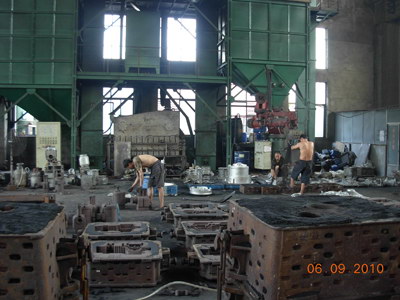
3. Self-Hardening of Resin Sand Mold
After molding by workers, the
sand is still loose. Then, the sand mold will be
coated by a type of alcohols based coating, after
burning, the resin sand mold will become very solid.
This is why this casting process is called as hard
mold casting process, also called as self-hardening
sand mold. All good characters of this casting
process are because of this hard mold.

3. Melting and Pouring
As same as green sand casting
process, both medium frequency electrical furnaces
and cupola furnaces could be used to melt irons for
resin sand casting process.
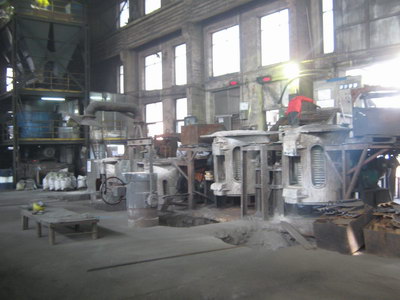
4. Sand Blasting, Cleaning and Grinding
After the hot iron castings are
taken out from sand molds, they will be sand blasted
to remove the sand, then the workers will cut off
the gating head, and grind the gating positions and
parting lines. Finally, the rough castings will be
completed.
If they need further machining
and coating, then these rough castings will be taken
to the machining or painting workshops.
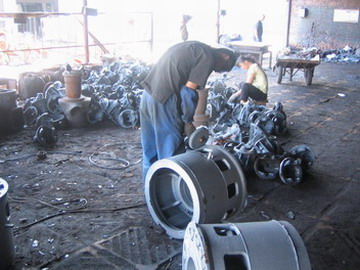
|