Casting deformation defect is a common problem in casting production, and its causes can be roughly divided into structure design issue, inside stress, unreasonable sand box, improper pouring riser, etc.
Causes of Casting Deformation:
(1) The casting structure design is unreasonable. The difference between the thickness of the casting wall is too large, which makes the cooling rate of the casting uneven, and affects the normal shrinkage and deformation of the casting;
(2) The shape and dimensions of the casting caused by the casting stress do not conform to drawings;
(3) The sand box structure design is unreasonable. The distance between the box stop and the convex part of the casting is too close, and the amount of sand is small, which hinders the normal shrinkage of the casting;
(4) Improper setting of pouring (riser) opening. The gate or riser is too close to the box stop or the convex part of the casting, and the amount of sand is small, which prevents the normal shrinkage of the casting;
(5) The core bone eats less sand or the core sand has poor retreat performance, which hinders the normal shrinkage of the casting after pouring;
(6) Premature boxing will cause the castings to cool rapidly and unevenly, which will affect the normal shrinkage of the castings and sometimes cause the castings to burst;
(7) The wooden mold material is not dried or the wooden mold structure is improperly made, and the setting position is incorrect. The size of the wooden mold is shrunk and the actual objects do not match the drawings;
(8) Slam the wooden mold when modeling, make the wooden mold bend and warp, and the cavity will be out of shape;
(9) The modeling sand is not balanced and uneven, and the wooden mold is skewed incorrectly;
(10) The sculptor disassembled the mold from the wooden mold, but did not put the mold in place when sculpting, and lacked a mold in the casting;
(11) After the wooden mold is finished, and the core box is made or not, the sculptor will not fit the clay core according to the wooden mold and cast a solid iron casting.
(12) When the casting enters the pit, the casting part is not placed properly, the middle is suspended or the triangle is effective, and the suspended part is not tightly pillowed, so that the casting is deformed during aging.
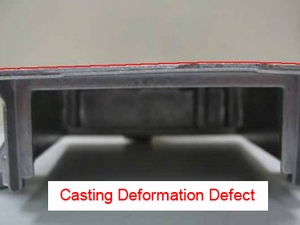
|