Lost wax investment castings made by silica sol, sodium silicate (water glass) and composite silica sol. Let us compare their advantages and disadvantages.
Silica Sol
Lost wax investment castings made by silica sol (binding material) is very expensive. This is because of the higher material costs, including the different wax, and also longer production leading time. Therefore, silica sol is only for smaller alloy steel castings with very high dimensional tolerance and surface quality.
Sodium Silicate (Water Glass)
Sodium silicate is also called as water glass in China, which is the cheaper binding material for investment castings. Using sodium silicate means much lower production costs and shorter production leading time. However, the castings' surface quality and dimensions made by it are not very good. Moreover, this binding material has certain pollution to environment, so it has been restricted by government.
Composite Silica Sol and Sodium Silicate
Our Dandong Foundry is using one type of composite silica sol. In other words, the inside layer is silica sol, the outside layer is sodium silicate. Therefore, it has good surface and low production cost. Using pure silica sol will cause 2 to 2.5 times higher production costs than composite silica sol.
The following is the steel casting made by composite silica sol process.
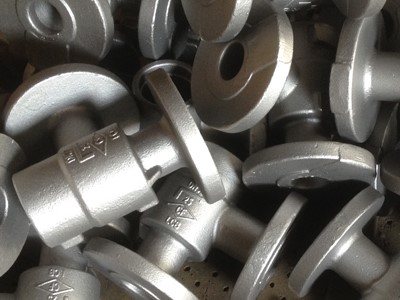 |