The most industrial valves can be broken down into the same basic components, such as valve body, valve bonnet, valve actuator, valve member and seat.
Valve Body
The body, or enclosure, of the valve is often the largest component. Material flows through the body between the ports, and all other valve components connect to it.
Depending on the type, size and complexity of the valve, valve bodies may be comprised of a single piece or be fabricated from several separate pieces. Modern casting processes that make use of cores allow the addition of complex inner cavities. These processes, including shell mold casting, investment casting and permanent mold casting, are often used for casting valves.
Valve Bonnet
The valve bonnet isn't necessary for every valve, but most standard industrial valves include this component. The bonnet attaches to the top of the valve body using either threads inside the valve body or bolts attached to flanges on both the body and the bonnet. The internal characteristics of the bonnet allow additional components to be attached, like the actuator and the valve member.
The bonnet often remains stationary while the valve is in use, but can be removed to service internal valve parts or to clear the body of obstructions. In some cases, the bonnet is combined with the body as a single part. Even if they are separate parts, the bonnet is often considered a characteristic of the overall enclosure. Without it, the material flowing through the valve would leak, and it would be impossible to actuate the valve.
Valve Actuator
Actuators are, in a way, the most important valve component. They provide the ability to control flow; without that ability, a valve is only a channel or a container. Actuators can be as simple as a hand wheel or a handle, or as complex as a computerized, automated valve controller.
Valve Member
The valve member is the component that directly prevents material from flowing through the body. Depending on the type of valve, the valve member can take on many shapes.
Valve Seat
The seat is a characteristic of the valve body that acts as a counterpart to the valve member. When a valve is sealed shut, the valve member and seat should be in full contact, and the connection should be tight enough so that no material can pass through.
Manufacturing Industrial Valves
Since valves are made up of a number of different parts, they cannot be manufactured using a single process. Metal casting is the method of choice to produce most valve components, but they nearly always need to be machined before they are finished.
In order to provide the greatest strength and sealing ability, valve bodies can be cast as single parts by using both molds and cores. Shell molding, investment casting and greensand casting all make it relatively easy to produce hollow parts with complex inner cavities. Because of this property, these three processes are often used for casting valves.
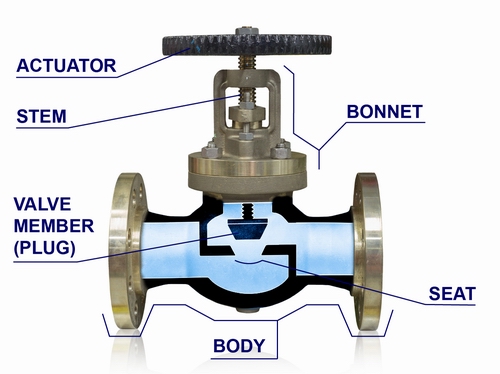
|