When machining the raw casting parts, some casting defects will be found, such as shrinkage, sand holes, segregation and other various defects.
These defects will cause high reject rate. If melted down, it will take many manual power, material resources and financial resources, etc..
So what can be done to reduce some casting defects?
1. High-quality melting
Before pouring, it is necessary to plan and check all smelting process. As per our customer's requirements, our engineers will plan and adopt the suitable production plan.
2. Avoid turbulent inclusions and control the flow rate.
If using the closed pouring system or producing the thin-walled casting parts, the flow rate of the smelting steel or iron should be increased appropriately, which means that the drop height of metal liquid can not exceed the critical value of the static drop height.
3. Avoid the air bubbles generated by the sand core or sand mold directly entering the liquid.
The sand core must maintain a relatively low gas content, and can also be vented to reduce the generation of pores in the sand core. Or the sand core can be completely dried, otherwise the clay or the base sand core mold repair glue is used.
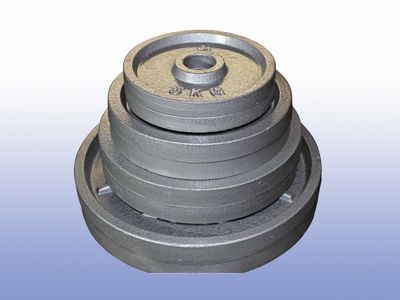
Counter weight raw casting parts
|