Corrosion is a major concern for metal casting customers. There are some methods to prevent or reduce corrosion on metal castings.
Proper planning
While no metal is fully corrosion proof in all environments, careful planning in the product design phase ensures maximum corrosion resistance within the service environment of each part. Beyond the material used, product designs may also include drainage channels and elements that improve air flow. Designers also know that crevices, gaps and blind holes can lead to corrosion.
Alloying
Alloying involves mixing metal elements together, often to improve qualities like strength, ductility and corrosion resistance. For example, combining iron with at least 12-13% chromium creates stainless steel, a widely used corrosion-resistant alloy.
Anodizing
Anodizing means oxidizing the surface of the metal in order to produce a protective oxide layer. Anodizing can add color and improve aesthetics, and is commonly used for aluminum products.
Heat Treatment
Proper heat treatment of castings plays a large part in how the material will perform in certain environments, including its corrosion resistance. Most austenitic stainless steel alloys require a solution-anneal step to solutionize any carbides present and prevent intergranular corrosion. Post-weld heat treatment is also very important to prevent similar desensitization of stainless alloys and intergranular attack during service.
Nitriding and Carbiding
Nitriding and carbiding are forms of specialized heat treatment that involve exposing the surface of a metal to a chemical environment that forms a protective layer on the surface of the part. Both techniques are primarily used to harden components, and a secondary benefit is a slight increase in corrosion resistance.
Regular maintenance
Visual inspection is key to prevent corrosion from affecting part performance. Regular maintenance to remove visible corrosion can dramatically increase part life within corrosive environments.
Galvanization
Galvanization involves coating the surface of a metal object with a layer of zinc. This zinc layer acts as a sacrificial anode to help prevent oxidative corrosion from attacking the original metal.
Painting and Powder Coating
Paint is often the most cost-effective way to protect against corrosion. Paint and powder coatings, often based on acrylic, nylon, vinyl or urethane, form a protective barrier between the metal and the corrosive elements such as water and oxygen.
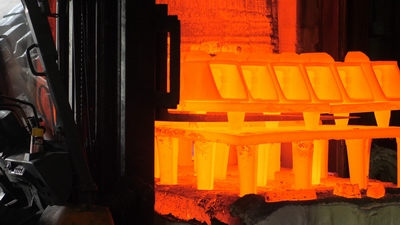
Metal casting heat treatment |