The cold shot, cold shut and misruns are the normal pouring metal defects. They are very harmful to the material quality.
Pouring metal defects arise during the process of pouring metal into the mold. If you have a pouring metal defect, it will fall into one of these categories:
Cold Shot
Cold shot is balls or drops loosely attached to the casting, left over from splatters of molten metal as it was being poured. Since they're smaller, the splatters cool before the rest of the casting and become embedded or attached.
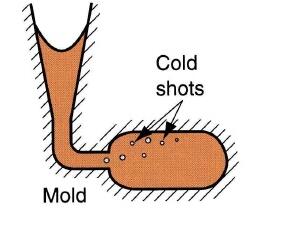
Cold Shut
Cold shuts occur when metal flows into a mold from two or more points, but it's too cold to merge into a seamless piece. That's when it creates a crack through the middle with rounded edges, which becomes a weak spot in the casting.
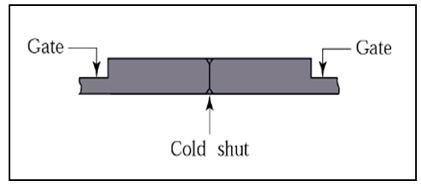
Misruns
Misruns, the close relatives of cold shuts, happen when the metal is so cool it solidifies before it can fill the entire mold. Misruns show up as castings with parts missing.
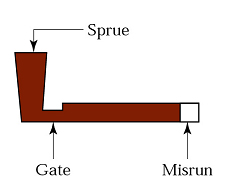
What Causes Pouring Metal Defects?
Defects from pouring the metal all stem from the overly cold temperature of the metal once it reaches the inside of the mold. These defects can be caused by simply pouring in metal when it's not hot enough. However, even with metal originally poured at the optimum temperature, defects can be caused by poor gating systems that allow the metal to cool off too much before it gets into the mold, or by mold sections that are too thin. Thin sections can solidify and block off other mold sections due to their thin size.
How to Prevent Pouring Metal Defects?
Pouring metal defects can, for the most part, be avoided by ensuring the molten metal stays warm enough to completely conform to the inside of the mold. The gating system can be redesigned to transport the molten metal faster, or to avoid sections that are thin enough to solidify before the metal can fill larger cavities beyond them. If that's not feasible, the pouring temperature can simply be increased.
Increasing the mold's gas permeability can also make the gases evacuate faster, so that the metal has less time to cool while still flowing into the mold. Cold shot specifically can be caused by careless pouring, so ensuring the metal is poured smoothly can also help with this problem.
|