|
The followings are the various factors caused the cracks on the grey iron castings.
These factors include metal composition, production conditions leading to high stress, knockout, felting and handling, and poor machining practice.
Metal Composition: |
- Low CEV for section thickness causing chill
- Lead>0.0004% can affect graphite and reduce strength
- Tin>0.1% embrittles the iron
- Insufficient manganese to balance sulphur (Mn%=1.7S%+0.3
)
Sulphur is a potent chill forming element
- Presence of carbide-promoting elements such as chromium
- Presence of antimony, boron and lead from enamelled scrap in the charge
|
Production conditions leading to high stress |
- Faults in running and gating system
- Restraint of strong cores surrounded by thin metal sections
- Fins of sand on cores producing notch effect
- Differential cooling of thick and thin wall sections producing high stresses
Rapid cooling
- Sharp corners and re-entrant angles between sections and at ingate to casting connection
|
- Sand, slag, laps and shrinkage acting as stress raisers
- Cracks in flash propagating into the casting
- Imperfect surface on chills and denseners causing restriction on contraction
- Rapid or uneven heating in stress-relief heat treatment
- Crossed joint causing cracking in thin sections
- Excessive shot-blasting
|
Knockout, felting & handling |
- Hammering to remove sand, runners, risers or flash
- Throwing castings into stillages
- Stacking castings in piles
- Inadequate care in handling stressed castings
|
Machining practice |
- Bad handing
- Excessive or uneven clamping
- Heavy cut and high machining speeds
- Poor condition of cutting tools
- Heat generation during rapid deep grinding, or insufficient flow of cooling lubricant
- Interrupted cut
|
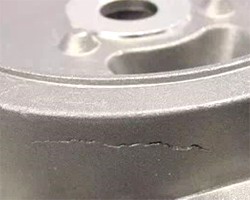
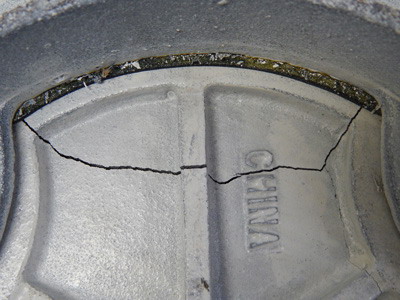
|
|