The right heavy-duty wheels are crucial to the smooth operation of any industrial application. Material is a key consideration in wheel selection.
As with any equipment, correct material selection depends on its specific use. Common choices include steel, cast steel, cast iron, ductile iron, and various steel alloys. It is important to understand the advantages and disadvantages of both steel and iron—and how it can benefit each application.
Track applications
In a track application, a metal wheel that is harder than the track will cause wear to the track. The harder metal will always outlast the softer metal. It is best to choose track wheels which are softer than the track material since it is more economical to replace wheels than the entire track. Heavy duty steel wheels are typically a better choice for use on a track in comparison to cast iron industrial wheels.
Steel vs Iron Wheels for a Track
Steel Wheels
More elastic and forgiving of track irregularities.
More durable on irregular tracks—safer, with less downtime.
Less frequent replacement of wheels.
Iron Wheels
More easily broken by irregular tracks (especially the flange of the wheel).
Less durable on irregular tracks—poses safety hazards, and longer downtime.
Frequent replacement of wheels.
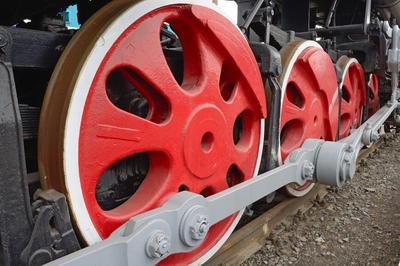
Steel track wheels are typically favored over iron track wheels as it
minimizes the damage caused to the track.
Wheel applications
Load
The choice between steel and iron wheels will depend on how the load is dispersed within a cart or vehicle. For loads that vary and shift, steel is favorable. For evenly dispersed loads, cast iron offers greater resistance to fatigue.
It is essential to keep in mind that regardless of the material chosen, the wheels must measure up to manufacturer limits. Remember to use a safe working load (SWL) standard, and consider the possibility that the load may be subject to harsh conditions and may require a heavier duty wheel than the SWL indicates.
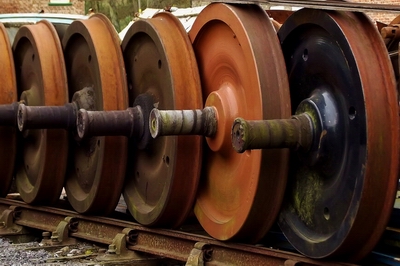
It is crucial that all industrial wheels measure up to manufacturer limits.
Use a safe working load (SWL) to verify load capacities in industrial applications.
Impact
The impact on the wheels must also be recognized. Some industrial wheels are constantly subjected to jarring high impact—often during loading or unloading. Constant high impact causes fatigue or fractures in the metal over time. Steel is more elastic than iron and can adapt better to stresses. For high impact situations, steel is the safer choice as it is less likely to shatter and pose a safety hazard.
An intermediate option to consider is ductile iron, with characteristics that are in-between that of cast iron and steel. Ductile iron has much more impact and fatigue resistance than cast iron, and is less likely to crack under stresses. In ductile iron, the graphite of the composition is in the form of nodules rather than flakes. This is different from cast iron where the sharpness of the graphite flakes can create stress points that result in cracks.
Stability
A wheel's elasticity helps to keep the load stable, and steel is more elastic than iron. If a load must be kept extremely stable, such as for a dry kiln lumber cart where lumber is stacked optimally for drying, steel wheels may be the best choice.
Cost
Cast iron wheels are typically less expensive to purchase than steel wheels. However, if the elasticity of steel is necessary for inconsistent tracks or varying loads—steel may be the more economical choice in the long run. The downtime, repairs, and replacements associated with iron wheels can quickly add to costs in the long term.
Extreme conditions
It is best to consult an engineer regarding materials if any equipment or application will be operating under extremely high or low temperatures. In these situations, heat treatment or a custom steel alloy may be used to ensure smooth operation in harsh conditions.
Exposure to substances
In some applications, metals will be exposed to corrosive chemicals, grease, and oil. In such applications, cast iron will tolerate these substances better than steel, all else being equal.
Aesthetics
Typically, aesthetics is not the focus in industrial applications. However, in situations where aesthetic appearance is important, cast iron is favorable as it is suitable for intricate designs. For example, wheels may be produced in iron or aluminum to use as historical reproductions or for solely decorative purposes.
Steel vs iron wheels
Consider these questions before making an informed choice between steel or iron wheels for any industrial application:
Quick checklist
Will the wheels be operating on a track?
Will the track be consistent or inconsistent with sharp turns and level variances?
Will the wheels be carrying constant or varying loads?
Will the wheels be subject to high impact?
Will the wheels be required to offer optimal stability?
Will the wheels be operating in harsh temperatures?
Will the wheels be in contact with harsh substances?
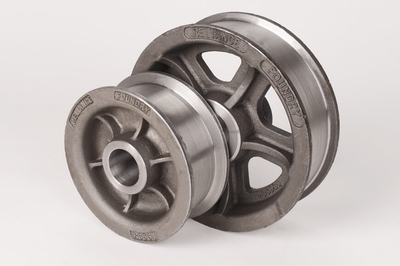
standard industrial wheels
This article was adapted from https://www.reliance-foundry.com/blog/wheels-iron-steel
|