How to control and inspect casting quality? This is a very key issue if you want to buy iron and steel castings from China.
Most of iron or steel foundries in China do not have completed quality control and inspection methods, moreover, the casting quality could be affected by many factors, therefore, after a while, you may meet some quality problems. This is a very normal situation.
The following methods will be very helpful to you:
1. Find one good supplier. This is very important!
One good supplier will have rich experience in quality control and inspection, especially, they will have completed quality management system. Please pay attention to this point. If someone has ISO 9001 certificate, it can not proof that they have good quality control. One certificate is not enough at all. In China, you can get the certificate easily, but it does not mean the manufacturer could control their quality accordingly.
If you find a good supplier, then they could complete all quality control and inspection before shipment, which will save you lots of money and time wasted on quality compensation.
If you use a poor supplier, you will have to use lots of time on quality inspection, and even after you have punished them very seriously, you will lose your end clients, or your marketing. The lost will be unbearable.
The key problem is: You do not know who is the good supplier at the beginning. Everyone will say we are the best, we will offer the lowest prices, and the best quality. So, you will be confused.
One client told us that they will try the supplier with the lowest price offer, if their quality is not good, then they will use us. However, you will face two risks.
A. When you choose someone, you will have to invest on the patterns. If you will not use them in the future, they may not give you these patterns, or they may request some compensation. Therefore, it is very difficult to change the suppliers.
B. At the beginning, or trial runs, all suppliers could control the quality very well, however, when the orders become larger, or after a while, their quality issues will come out, even if they want to improve, you may have to face huge compensation or lost from your clients.
All in all, choosing a good supplier is very important. If you make a mistake at this step, then all following steps will be wrong.
2. Checking the inside quality report of your supplier.
Some clients may request quality reports, such as dimensional report, or material certificate. Actually, these reports are not very useful, because your suppliers may not be honest for all data. Of course, one good supplier should be honest.
One good supplier should have their own inside quality report system. For example, our Dandong foundry has our inside quality inspection reports, including dimensions, key quality issues, visual and defects inspection reports, material inspection etc., we also have our own technical file for common problems specifically to your products. Our inspectors will use these inside reports to complete all related inspection, then these reports will be signed by quality manager. All these reports must be completed and signed before delivery.
We have lots of experience to the inside report system, after many years, we find this report system is very useful.
If you just want your supplier to issue one English report to you, you do not know if they have performed completed quality inspection. One dimensional report can not represent all quality issues at all.
Of course, you can not read these inside reports, but if you can assure that your suppliers are using it, then will be good enough. One completed inside quality report system may be a good judgment to good suppliers.
3. Asking for the photos before delivery.
As for the new suppliers, you could ask for some photos before packing or before shipment. The photos could reflect some visual problems and surface defects, so this will be helpful for you to control some quality issues.
Of course, your supplier may not be happy to do these works, however, at the beginning, these works are very important, it could save lots of time and sample delivery costs. I believe that one good supplier will be willing to do so.
4. Do some quality inspection before acceptance.
When you receive the casting products, you should do some inspection as far as you could, such as the key dimensions, visual inspection for the normal casting defects. As for the normal casting defects, please refer to our article "Casting Defects".
There may be some very rust problem, or some obvious surface problems when you receive them. If you send them directly to your end users or final clients, you may lose your face.
These quality control and inspection methods will be very useful for cast iron and cast steel casting parts. These are many years' experience of our Dandong foundry.
We are not saying that we are doing very well, and other Chinese foundries are doing very bad. Actually, our foundry also has some problems, however, we are improving our quality system constantly, and sincerely hope that we could supply better casting products.
You must be tired after reading this article. Show you something good! This is the metallograph of ductile iron. Are they interesting? The metallograph is the most important quality inspection method for ductile iron castings. - Written by Galen Wang.
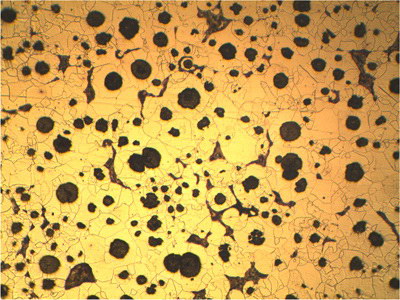
Home Page |
Casting Products |
Contact Us |