Pulley refers to either a sheave or a sprocket. Sprockets are toothed for higher-torque applications, while sheaves have grooves and are usually used with V-belts.
Pulleys can be made of various materials, including ductile iron, anodized aluminum, and steel.
When selecting a material for a sheave or sprocket, designers should consider the number of parts needed and application, including any special requirements such as corrosion resistance, heat conduction, static conductivity, wear resistance, and low operating noise.
Industrial sheaves and sprockets -- collectively called pulleys -- are typically made of gray iron or ductile iron. These materials offer excellent wear resistance, machinability, heat dissipation, and damping.
The tensile strength of a sheave or sprocket determines rim speed. The higher the tensile strength, the faster the component can be run. Elongation relates to a material's ability to withstand shock loads. The higher the elongation, the more shock load a sheave or sprocket can withstand.
An important characteristic of both ductile iron and steel is their ability to withstand heavy shock loads. This property, known as elongation, gives these materials much better shock resistance than gray iron, which is more brittle and likely to break when over-stressed.
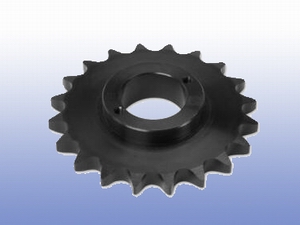
Cast Iron Sheaves and Cast Iron Sprockets
|