SiMo Ductile Iron is suitable for making various casting parts with high temperature resistance property, such as auto exhaust manifolds.
By increasing the Silicon and Molybdenum content of Ductile Iron, the heat resistance and strength at high temperatures will be increased significantly.
The following is the typical chemical composition:
C=3.2-3.8%, Si=4.0-5.0%, S < 0.02%, Mg=0.03-0.07%, Mo=0.5-1.5%
Physical properties depend on temperatures, the typical values are detailed in the table below:
Temperature oC |
Tensile Strength N/mm2 |
0.2% Proof Stress N/mm2 |
Modulus of Elasticity N/m x 104 |
Hardness BHN |
23 |
550 |
480 |
14.8 |
(200-240) |
300 |
480 |
395 |
14 |
|
500 |
350 |
270 |
12 |
|
800 |
50 |
30 |
2.5 |
|
The main application for SiMo is in Automotive Exhaust and Turbocharger Systems, such as cast iron exhaust manifolds, but it is suitable for any high temperature application where both strength and ductility are required.
Machineability is similar to that of EN-GJS-500-7.
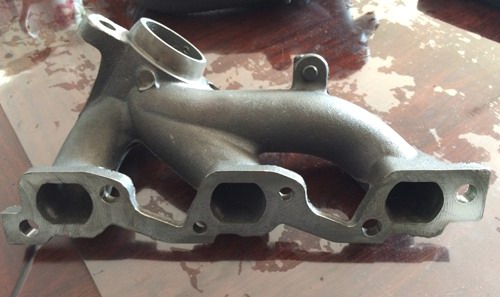
SiMo Ductile Iron Exhaust Manifold
Typical Microstructure
The following photo is the typical microstructure of SiMo ductile iron. The black and round balls are the spheroidal graphite, the light yellow is the ferrite, the dark yellow is the pearlite.
Certian content of pearlite will increase its tensile strength and hardness. More spheroidal graphite balls will be good ductile iron.
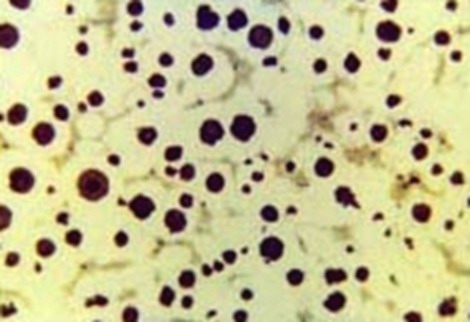
Guideline Figures for Maximum Exhaust Manifold and Exhaust Gas Temperatures
Material Grade |
Max. Manifold Temperature °C |
Max. Exhaust Gas Temperature °C |
EN-GJS-400-15 |
700 |
770 |
EN-GJS-SiMo (0.5% Mo) |
750 |
820 |
EN-GJS-SiMo (1.0% Mo) |
780 |
820 |
EN-GJS-SiMoNi |
795 |
835 |
Ni Resist D-5S |
870 |
950 |
|