Hand Molding Method of Sand Casting
Sand casting production
mainly include hand molding and machine molding method. The
operation of hand molding is more simple and flexible, but the
production rate is low, so it is suitable for small batch, amount
production in dandong foundry.
Hand Molding (Manual Moulding) Methods
1. Whole pattern, two cases molding
When the largest cross section of casting parts is located on the
top position, then this position could be used as the parting
surface, and the pattern could be made as a whole part as the
following diagram.
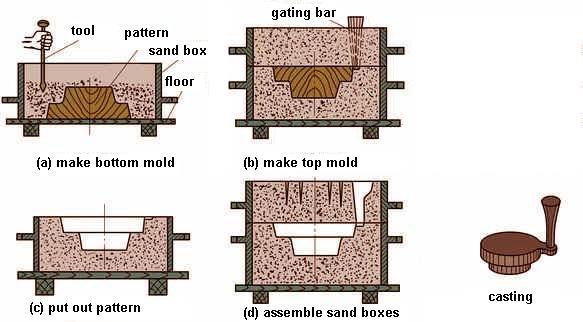
The whole pattern is in the sand mold, so it can avoid
mismatch of mold cases,
and can guarantee the high dimensional accuracy.
2. Two parts molding
The patterns could be designed as two separated parts, and could be
assembled with stop bolts as following.
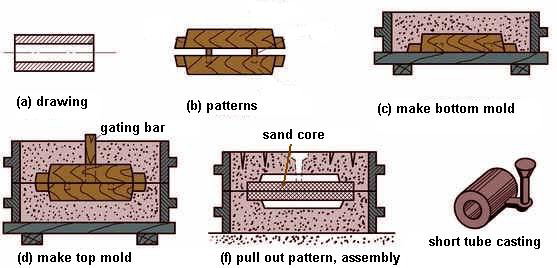
This molding method is simple and has very wide application.
However, if the sand mold
cases (sand boxes) could not be fixed accurately, then
mismatch will happen, and it will affect the accuracy of castings.
Moreover, the parting line will affect the surface quality too.
3. Dig sand molding
When the largest cross section is not located on the end positions,
and the patterns are not suitable to split into two parts, then dig
sand molding could be usable.
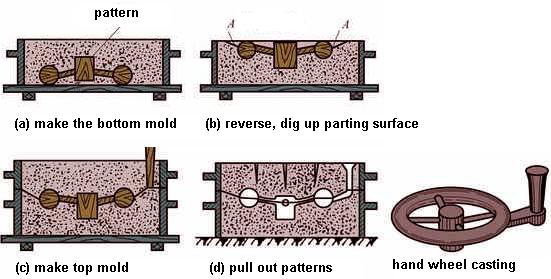
The molding method needs workers to dig up the parting surfaces in
order to put out patterns.
The operation is troublesome and needs high operation skills. So, it
is only suitable for small batch of casting production.
4. Patterns with loose pieces
If the side face of casting affects the draft of patterns, then we
can make some loose pieces fixed on the patterns. So, after molding,
we can pull out the main part of patterns firstly, then pull out the
loose pieces.
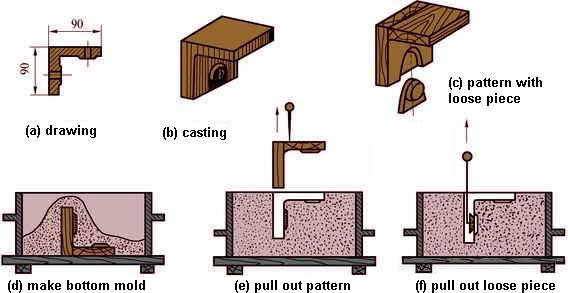
This molding method requests to make the sand very tight, otherwise,
when pull out the main patterns, the loose pieces may damage the
nearby sand molds. This method is only suitable for producing small
amount of castings. Refer to iron-foundry.com.
5. Sweep molding
Sweep molding uses the scraper blade to replace normal patterns. The
scraper blade could rotate with the fixed shaft, so could make the
round sand molds with the designed shapes.
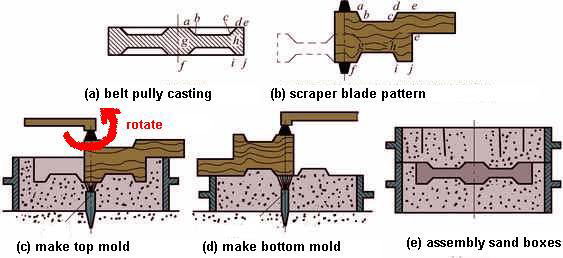
This molding method could reduce the pattern costs, but the
operation needs more skills, and the production rate is very low. In
addition, it has strict requirements to the shapes of castings. This
method normally was used to produce axially symmetrical castings,
such as flywheel and rings.
6. Multiple-part molding
Three part molding is also called as multiple-part molding, which
will use three or more sand boxes (flasks) to produce one casting.
If the two ends of casting have larger cross sections than middle
position, then two-part molding will not be able to produce it. The
following is the molding diagram for scored pulley casting by three
part molding method.
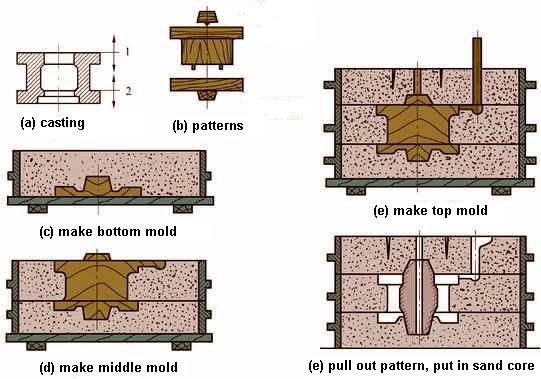
This method needs three or more parts of patterns assembled. There
will be two parting surfaces. The molding process is complex and so
lower production rate. The mismatch of sand flasks will be easier to
happen. So, it only is suitable to produce
small amount
castings.
Home |
More Articles |