Sand Casting
Sand casting means
the production processes that need sand as the main molding
material, it also means the casting products made by these
processes.
1. Casting
Process
We need make
wooden, resin or
metal patterns according to the drawings or samples. Then,
we put patterns into the sand boxes, then put green sand or resin
sand into the boxes, then make the sand become solid by pressure
come from molding machines or manual methods, then take the patterns
out, and so, the space taken by patterns will become hollow, then
inject melted liquid iron into the hollow space, then after cooling,
the hot iron water will become iron parts, the after sand blasting
process, remove the sand on the surfaces, and we will get the clean
cast iron parts.
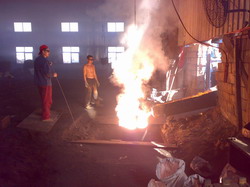
2. Casting
Prices
The prices of sand
castings depends on rough casting cost, machining cost, surface
coating cost, heat treatment, packing and delivery costs. You could
find the FOB China prices on the main page of
Dandong Foundry in China.
The prices of
exported sand castings will be mainly affected by the exchange rate
of USD to RMB and pig iron prices. Therefore, the prices are not
stable.
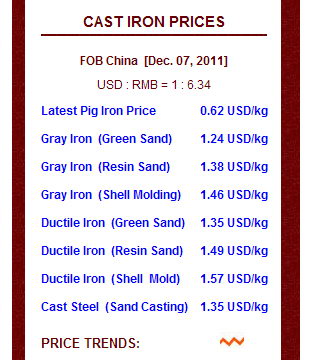
3. Main
Equipments
There are many
equipments for producing sand castings.
3.1. Pattern
Making
Normally,
metal foundries
do not make wooden and resin
patterns in-house. However, some large foundries with
machining capability could make the metal patterns by themselves.
But as for the complex metal patterns, only the professional pattern
workshops could meet the requirements.
As for wooden and
resin patterns, the workshops need some manual tools and simple
lathes. As for metal patterns, the workshops needs some CNC centers,
numerical control milling machines, wire-electrode cuttings.
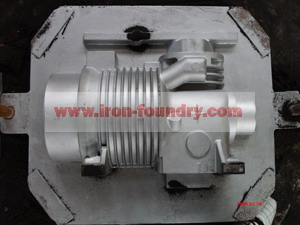
3.2. Molding
Equipments
3.2.1.
Manual molding, it is very
traditional molding method, which is also called as hand molding.
Workers use simple tools and sand boxes to complete the molding
process. This method still has very wide application. Almost all
metal foundries are still using this method to deal with small batch
production or special sizes of castings.
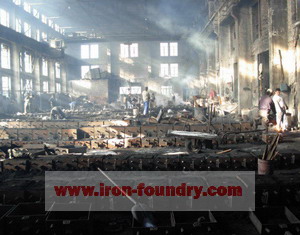
3.2.2. Molding
machines. These machines include mechanical molding machines or
simple Leak mould machine. Leak mould machines do not have wide
application since their low production rate and dimensional
restriction. Molding machines are still widely used, they have their
advantages, however, because of their comparatively low production
rate, they have been replaced by automatic molding line step by
step.
3.2.3. Automatic molding lines.
These molding lines have very high production rate, so more and more
iron foundries are importing them, and they are perfect for
producing automotive parts.
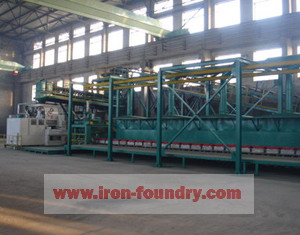
3.3. Cleaning
and Grinding Equipments
3.3.1. Sand
blasting equipments are the main cleaning equipments, and there are
mainly hook-type, crawler, transfer desktop shot blasting machines.
After sand blasting, the castings will need workers to grind them by
grinding tools to remove the burrs and sharp edges.
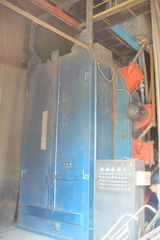
3.4. Furnaces
The melting
furnaces main include medium frequency induction furnace and
traditional cupola. More and more metal foundries have imported
induction furnaces to replace cupola in order to improve the
production rate and casting quality.
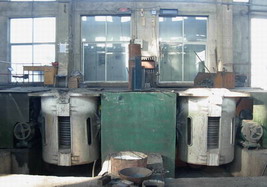
Machining
Equipments
3.4.1. Most of
metal foundries in China have their own machining equipments
in-house. At least, they could complete the simple or rough
machining by themselves. Some larger foundries have high precision
machining tools.
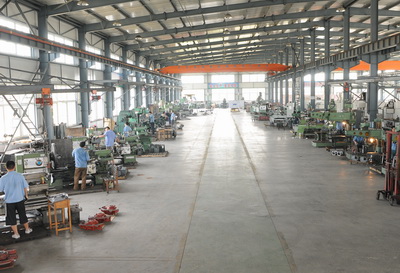
4. Materials
Foundry sand is the
main molding material for sand castings. The main sands include
green sand,
resin sand, pre-coated resin
sand and water glass quartz sand.
According to the
metal materials, sand casting can be divided into cast iron, cast
steel, cast aluminum, cast bronze castings.
5. Casting
Defects
Sand castings have
many defects, such as sand holes, air holes, sand inclusion, cold
shut, shrinkage, cracks etc. Less
casting defects
will be the main quality issue.
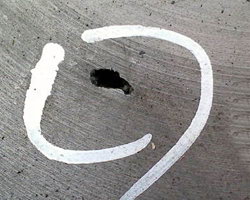
6. Casting
Products
Sand castings could
be widely used for many industrial and residential fields, mainly
include stove and boiler parts,
agricultural and engineering
machinery parts, pump and
valve bodies, pipe
fittings, drainage parts etc.
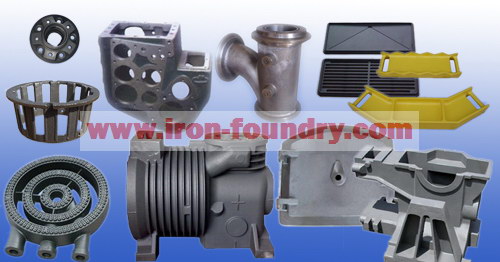
7. Quality
Inspection
Metal foundries
normally completes the
visual inspection,
dimensional inspection, physical properties (hardness, tensile
strength) and chemical component. As for some special tests, such as
the sharp impact test, pressure test, x-ray inspection, magnaflux
inspection and ultrasonic test, some professional suppliers could
complete them in-house, but most of suppliers will have to entrust
professional labs.
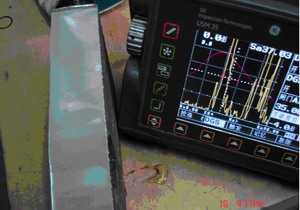
8. Casting
Suppliers
In China, there are
some different metal
castings suppliers. Some are professional machining
workshops, but they have their foundry partners. Some are
professional metal foundries. Some are just trading companies, which
have their own sub-suppliers.
Sand casting process
has thousands of years history, and the products made by this
process have taken over 80% of total castings in the world nowadays.
Home |
More Articles |