|
Gas Burner
Gas burner is also called as stove
burner or gas stove burner. We have
produced gas burners for years in China,
so always wanted to write an article for
burner buyers to learn about all issues
related with gas burners.
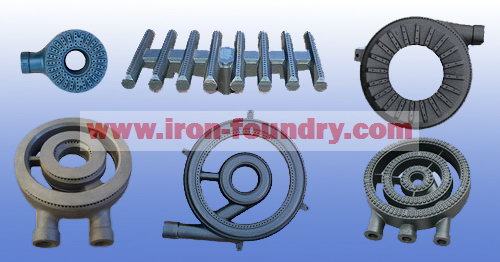
Gas Burner Application
Gas burners are the fuel gas combustion
devices, which make the fuel gas and air
separately or mixed into the combustion
zone to achieve stable combustion. The
fuel gases include acetylene, natural
gas or propane. Gas burners are widely
used in residential and industrial
areas, from ordinary kitchen stoves to
hospitals, restaurants, outdoor
barbecues, industrial furnaces and
boilers etc.
Gas Burner Types
There are hundreds types of gas burners.
We just can list some of them, such as
portable stove burner, outdoor gas
burner, natural gas burner, propane gas
burner, burner head, large burner, small
burner, star burner, single gas burner,
rectangular stove burner, wok gas
burner, camping gas burner, double gas
burner, fireplace gas burner, portable
gas stove burner, lp gas burner,
commercial gas burner, butane gas burner
etc.
Gas Burner Material
According to our experience, the most of
gas burners will use the gray cast iron
ASTM A48
Class20 or Class30, but seldom Class35.
Why, because the small fire vent holes
need machining, if the hardness of
material is too high, it will be
difficult to drill. You can not compare
these holes with other normal holes,
drilling on the small buttons will be
much more difficult. Moreover, the
strength of class20 should already be
enough for the application.
If you want to learn the details about
these material degrees by other
standards, such as Germany, Japan, UK or
ISO, please check here
material comparison of gray cast iron.
ASTM A48 Class 20 is equal to GG15,
HT150, FC150, ISO150.
ASTM A48 Class 30 is equal to GG20,
HT200, FC200, ISO200.
ASTM A48 Class 35 is equal to GG25,
HT250, FC250, ISO250.
Some buyers may choose the higher degree
to get stronger parts, we do not suggest
this practice. Higher degree will cause
more difficulty for production, and so
higher defective rate, and so for higher
costs. As for the gas stove burners, the
over-high tensile strength is
unnecessary.
Gas Burner Casting
Process
According to our experience, we suggest
two casting processes for producing the
gas burners. One is green sand for the
shell, and resin sand for the core. We
made the core by
shell
molding process, which means we
made the pre-coated resin sand core,
then use the normal
floor
molding with green sand for
producing the outside shell. In the way,
the inside surfaces are good, and
outside surfaces are normal. This
process can meet your requirements by
the lowest production costs. Of course,
the green sand must be very fine, normal
coarse sand is unacceptable.
Another process is making both of the
shell and core by pre-coated resin sand
and shell molding process. In the way,
both inside and outside surfaces are
good, but just higher production costs.
So, the buyers should choose the
suitable casting process according to
the specific application.
Gas Burner Machining
The only issue about gas burner
machining is the machining to the fire
vent holes. Sometimes, there are dozens
to hundreds of fire vent holes on the
gas burners. They need drilling. If you
are failed to drill one of them, then
this gas burner will be failed,
therefore, the drilling is not an easy
work as your thought.
Dandong Foundry used several
small drilling machines to drill them.
There are several workers were just in
charge of drilling these small holes
everyday.
Gas Burner Patterns
As for the
casting patterns of gas burners.
According to our experience, we suggest
to use the iron patterns for making the
resin cores, and use the aluminum
patterns for making the shells of gas
burners. However, for the better outside
surface quality, you should consider to
use the resin sand for the shells, then
you have to use the iron patterns for
the shells. All in all, metal patterns
are necessary for the gas burners.
Gas Burner Surface
Coating
There are several types of surface
coating for the gas burners. One is the
black heat-resistant painting, another
is the normal black painting, which is
cheaper than heat-resistant panting, the
third type coating is using the
anti-rust oil. The heat-resistant
painting is the most expensive coating,
it is about 0.23 to 0.25 USD/kg. If your
gas burner is weight 1kg, then its
heat-resistant painting is about 0.23 to
0.25 USD/pcs.
Gas Burner Suppliers
Although many
iron
foundries can produce gas
burners, but not all of them could
produce them by low prices and produce
them very well. It is mainly because
they should use the fine sands and
should have the experiences to drilling
so many and small holes. Most important
of all, they should be very careful
during the casting, cleaning and
machining processes. Any sloppy
operation will cause the failure.
Therefore, it is difficult to find a
good gas burner supplier.
Gas Burner Prices
The prices of gas burners are mainly
related with the unit weight (especially
the rough casting weight), the numbers
of vent holes, the complexity of
structure, and the surface quality of
outside surfaces.
Gas Burner Defects
The main defects of gas stove burners
are will the sand holes on the surfaces,
usually allowable for 2mm diameter and
1mm depth sand holes, and the damage of
vent holes, and the dirty surfaces with
sand residues. Please notice that
normally welding is not permitted since
the stove burners should be air proof.
Home Page |
Casting Products |
Contact Us |
|