|
Introducing the pattern for casting process
Before production, metal foundries need to
make the patterns for the
casting process, and then use the pattern to produce many
casting molds, then use the molds to produce the
metal castings. So, one set
of pattern can produce many casting molds, and one casting mold can
produce one metal casting.
There are several types of patterns for casting production.
1. Wooden patterns
Wooden pattern is the cheapest casting
pattern. When metal foundries start to make the casting samples,
they usually use the wooden patterns. It is not only because of its
low cost, but also because they are easily to be modified again and
again till they are qualified.
However, wooden pattern is very soft and
has low strength, and most of them are made by hand, so they can not
be used for batch production and their dimensional and surface
quality are not very good.
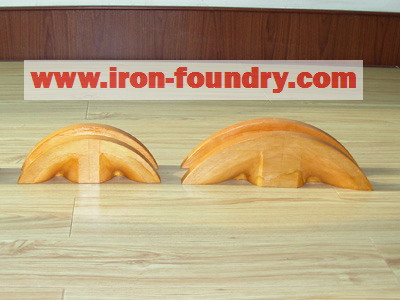
2. Resin patterns
Resin pattern is very common for sand
casting process. Resin pattern is made by epoxy resin and fiber
glass clothes. So, resin patterns have good strength and lifetime,
and can produce thousands of casting molds. Their dimensional and
surface quality are better than wooden patterns, and their cost is
not high.
However, you have to use the wooden
pattern to make the resin pattern, so the metal foundries usually
use the wooden pattern to make the samples, and use the resin
patterns for the batch production.
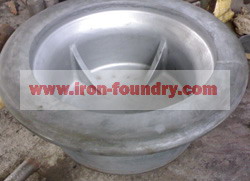
3. Metal patterns
Metal patterns have many advantages.
Such as, better dimensions since the metal patterns are usually made
by the CNC centers
or digital milling machines, better surface quality, and higher
strength, so have very long lifetime. Moreover, for some special
casting processes such as
die casting,
shell molding process,
automatic molding lines,
the metal patterns are the only choice.
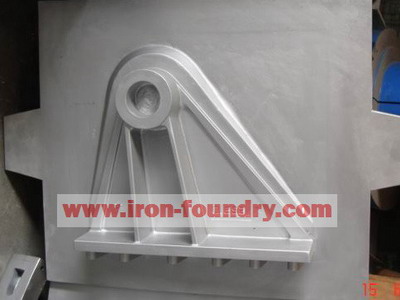
For example, as for the die casting and
shell molding process, the patterns need to bear the high
temperature for the hot liquid aluminum or hot resin sands,
therefore, the iron patterns are necessary.
As for the automatic molding lines, the aluminum and iron patterns
are needed to bear the high pressure and frequent works.
As for the
lost-foam casting (LFC) process, the metal foundries need to
make the metal patterns, and then use the pattern to melt the foam,
then produce many foam molds.
As for the
permanent mold casting process, the heat-resistant steel
patterns are the needed to produce the metal castings.
Moreover, as for some complex castings, hand-made patterns can not
meet the dimensions and structure requirements, so the metal
patterns will be needed.
The disadvantages of metal patterns are the long lead time for the
patterns, one set of metal pattern usually need about 25 to 30 days
to complete, and the very high costs. The cost of one set metal
pattern is usually from 800 USD to 5000 USD according to the size
and complexity.
According to the experience of
Dandong Foundry in China, the buyers and foundries need
to consider all aspects for the casting products, then choose the
most suitable pattern for the castings.
Home |
More Articles |
|