|
Inspection Methods to Ductile Iron Castings
Normal casting defects of ductile iron
include some macro-defects, such as air holes, sand inclusion, slag
inclusion, shrinkage
or shrinkage cavity, and some micro-defects, such as unqualified
nodularity rate and too large grain size, etc.
The inspection methods to ductile
iron castings include visual inspection, magnetic powder
test and ultrasonic test.
1. Visual Inspection
Visual inspection is the most heavy
works, they need lots of grinding works accompanied. Normally, the
visual inspection require to meet the following requirements:
a) No cracks, no welding treatment, no
sand or slag inclusion.
b) No obvious sand holes or air holes. As for allowable sizes and
amount for the air and sand holes, you could refer to the other
articles in Dandong Foundry Blog. As
for the different castings, there are different requirements.
c) No cold flake or mismatch defects.
d) No machining scratch or impression.
During visual inspection, it is hard to
distinguish the air holes and sand holes. Air holes normally have
smooth inside surfaces, and have regular shapes, but sand holes have
irregular shapes and have dirt or sand residues inside. As for the
air holes, since they are shallow, the inspector could measure their
sizes, and check if they are allowable, but for the sand residues,
most of them will cause deeper damages to the castings, so they
should be grinded or repaired before acceptance.
Moreover, the inspector should check the sand blasting. The
inadequate sand blasting will cause the rough surface quality, or
even leave the oxide skin. These situation should be sand blasted
again or be grinded further.
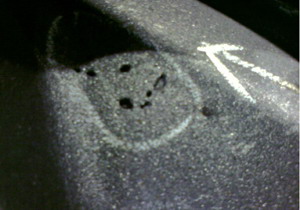
2. Magnetic Particle
(Powder) Inspection
Magnetic particle inspection is a kind
of
NDT testing. The florescent magnetic particle testing is
suitable for ductile iron castings. According to our experience,
both the water base magnetic flaw detection ink and dry magnetic
particle are suitable for inspection to ductile iron. Since the
surface smoothness has large effects to the inspection results, so
you could try to grind the surfaces to improve the inspection
sensitivity. Normally, the casting head areas easily have defects.
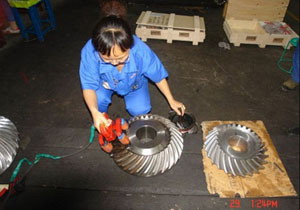
2. Ultrasonic Testing
Ultrasonic testing is also an inspection
method to ductile iron castings. It could inspect not only air holes
and sand holes, but also inspect the slag inclusion, cracks and
other material defects. However, comparing with the cast steel,
forged or welding parts, ultrasonic testing to ductile iron castings
has high difficulties, and the results need careful and skillful
identification. It is because ductile iron has more complex inside
structures. Some structures may cause the wrong judgments, and
moreover, the surface quality has some effects to accuracy of
inspection results.
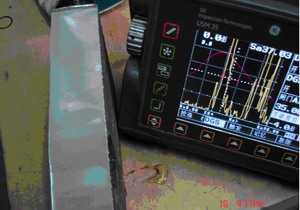
Home |
More Articles |
|