|
Advantages and
disadvantages of manual green sand molding and automatic molding
line
Manual green sand casting process is very
common in China foundries, and automatic molding is very advanced,
so we will introduce their differences, advantages and disadvantages
for producing iron castings.
1. Manual green sand casting
Green sand is also called as wet sand, the main content is silica
sand and clay. Molding process was completed by pure manpower. This
is the most traditional casting process, however, this is still
widely used in China foundries.
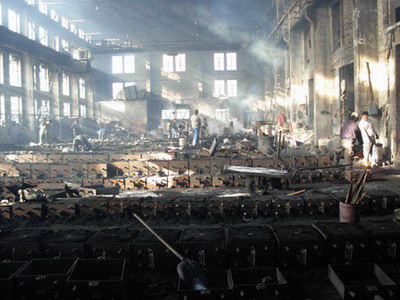
Advantages:
a) Simple molding equipments, low technique requirements.
b) Low production costs, so lower casting prices.
c) Flexible products, it could produce very small or very large
casting parts.
Disadvantages:
a) The castings have low dimensional tolerance, not very good
surface quality.
b) More surface and inside casting defects than other casting
processes.
2. Automatic molding line
Automatic molding line could complete all molding, cleaning, sand
recycling works automatically, so it could have very high production
rate and also save lots of manpower.
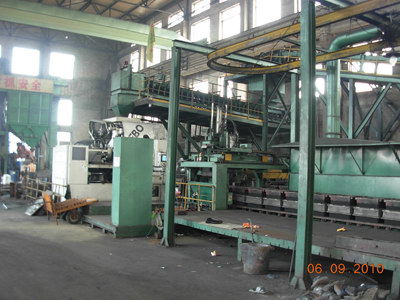
Advantages:
a) Automatic molding has very high production rate, so suitable for
producing automotive parts.
b) It can keep high dimensional tolerance, make the sizes accurate,
so reduce machining works.
c) It can make the quality more stable, better surface quality and
much less casting defects.
d) The molding material is still green sand, so its casting price is
low.
Disadvantages:
a) Because of the fixed sand flasks, so it can not be use to produce
large casting parts.
b) The pattern cost is high, so not suitable to produce small-lot
production.
c) It can not be used to produce castings with too complex inside
structures.
d) Normally, it can only produce iron castings, and can not be used
to produce aluminum and steel castings.
Hope this information could help buyers to know how to choose the
most suitable casting methods for your products. Thank you. Galen
Wang, Dandong Foundry in China.
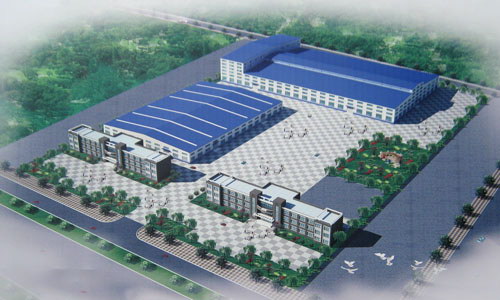
Home |
More Articles |
|