Ductile Iron and Gray
Iron Exhaust Manifold
(
Foundry in China)
Dandong Foundry has manufactured
various ductile iron and gray iron exhaust manifolds in China. We
have rich experience in casting production, machining, assembly and
quality inspection. Our foundry has supplied cast iron exhaust
manifolds for our aftermarket clients in USA, UK and Australia for
many years.
Ductile Iron Exhaust Manifolds,
product photos
Advantages of ductile iron exhaust manifolds:
1. High tensile strength and elongation, so strong enough for tough
working condition.
Disadvantages of ductile iron exhaust manifolds:
1. High production costs, so caused high product prices, about 5% to
10% higher than gray iron manifolds.
2. More casting defects, so caused high defective rate, difficult
for foundry production.
The followings are the manifolds made by ductile iron:
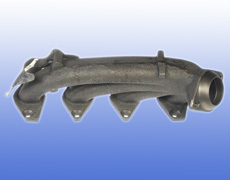 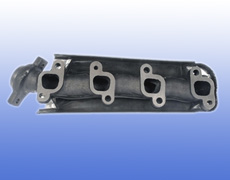
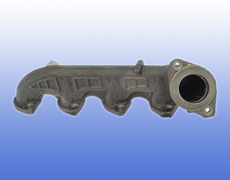 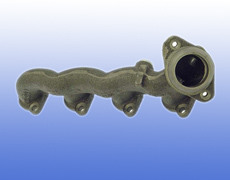 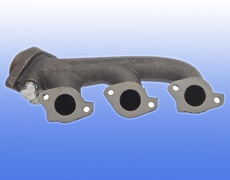
The following list is showing the common ductile iron material
grades for exhaust manifolds.
ISO |
ISO 1083 |
400-15 |
450-10 |
500-7 |
400-18 |
China
|
GB 1348 |
QT400-18 |
QT450-10 |
QT500-7 |
USA
|
ASTM A536 |
60-40-18 |
60-42-10 |
70-50-05 |
65-45-12 |
Germany
|
DIN 1693 |
GGG40 |
— |
GGG50 |
Austria
|
European |
EN 1563 |
EN-GJS-400-15 |
EN-GJS-450-10 |
EN-GJS-500-7 |
EN-GJS-400-18 |
Japan
|
JIS G5502 |
FCD400 |
FCD450 |
FCD500 |
Italy
|
UNI 4544 |
GS370-17 |
GS400-12 |
GS500-7 |
France
|
NF A32-201 |
FGS370-17 |
FGS400-12 |
FGS500-7 |
UK
|
BS 2789 |
400/17 |
420/12 |
500/7 |
India
|
IS 1865 |
SG370/17 |
SG400/12 |
SG500/7 |
Spain
|
UNF |
FGE38-17 |
FGE42-12 |
FGE50-7 |
Belgium
|
NBN 830-02 |
FNG38-17 |
FNG42-12 |
FNG50-7 |
Australia
|
AS 1831 |
300-17 |
— |
500-7 |
400-12 |
Sweden
|
SS 14 07 |
0717-02 |
— |
0727-02 |
Norway
|
NS11 301 |
SJK-400.3 |
— |
SJK-500 |
SJK-400 |
Gray Iron Exhaust Manifolds, product photos
Many types of exhaust manifolds were produced by gray cast iron.
This is because of their some advantages.
Advantages of gray iron exhaust manifolds:
1. Low production costs, so low prices.
2. Less shrinkage defects, so low defective rates. Foundry’s favor.
Disadvantages of gray iron exhaust manifolds:
1. Low tensile strength and elongation, so not tough enough for
severe working condition.
2. Require the manifolds have enough wall thickness; otherwise, it
will be too fragile.
The following is the exhaust manifold made
by gray cast iron:

The following
list is showing the common gray iron material grades for exhaust
manifolds.
ISO |
ISO 185 |
200 |
250 |
China |
GB 9439 |
HT200 |
HT250 |
USA |
ASTM A48 |
NO.30 |
NO.35 |
Germany |
DIN 1691 |
GG20 |
GG25 |
Austria |
European |
EN 1561 |
EN-GJL-200 |
EN-GJL-250 |
Japan |
JIS G5501 |
FC200 |
FC250 |
Italy |
UNI 5007 |
G20 |
G25 |
France |
NF A32-101 |
FGL200 |
FGL250 |
UK |
BS 1452 |
200 |
250 |
India |
IS 210 |
FG200 |
FG260 |
Spain |
UNF |
FG20 |
FG25 |
Belgium |
NBN 830-01 |
FGG20 |
FGG25 |
Australia |
AS 1830 |
T220 |
T260 |
Sweden |
SS 14 01 |
O120 |
O125 |
Norway |
NS11 100 |
SJG200 |
SJG250 |
Foundry production processes for iron manifolds
There are two types of foundry processes for cast iron manifolds:
1. Green sand shell and pre-coated resin sand cores.
This casting process could also be called as green sand casting
process; it could be used for making not very complex manifolds,
especially for gray iron manifolds. The production costs are lower,
but the surface quality of castings is not very good. There will be
more surface defects.
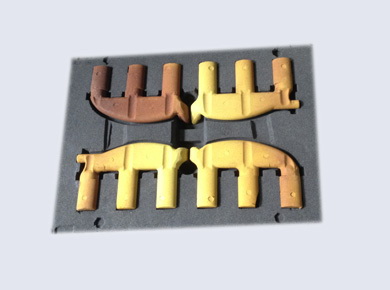
2. Pre-coated resin sand shell and cores.
This casting process is also called as shell molding process. It
could be used for making complex manifolds. The production cost is
higher, but there will be less surface defects. If the foundry could
control the production very well, its surface quality will be good.
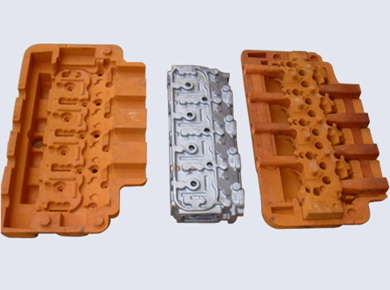
Frequent quality problems for cast iron manifolds
1. Cold lap is common defect for ductile iron exhaust manifolds made
by shell molding process. The foundry could solve this problem by
improving the gating design, molten iron temperature, or warm
keeping methods.
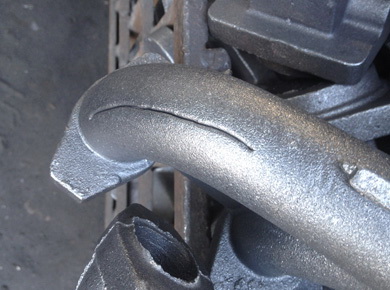
2. Surface sand holes, pin holes, air holes. These defects are
inevitable sometimes. For some defects on the surface, some filler
or welding could be used, but for some deeper defects, just scrap
them.
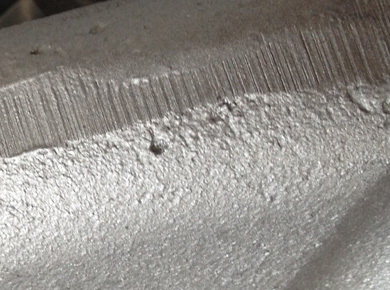
3. Shrinkage defect is very harmful for manifolds, you may see some
defects on the surface, but actually, it could go inside until
penetration.
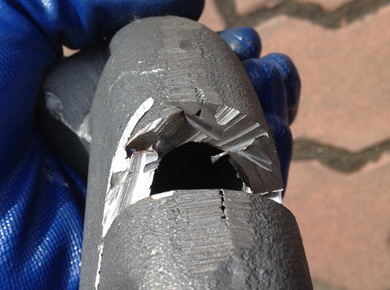
4. Mismatch problem. The manifolds will be assembled with some pads,
so if there is this problem, it will affect the assembly.
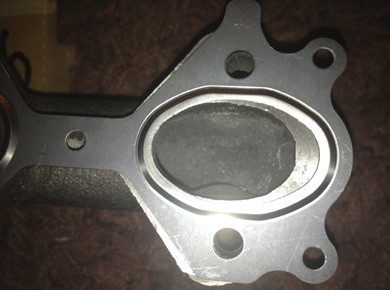
How to guarantee the manifolds quality for aftermarket?
1. 100% inspection before packing for all defects and problems. Once
the manifolds were packed, there will be no method to find the
problems. The products will be sent to final users, so will cause
reputation damage. Therefore, 100% inspection by specified inspector
will be the only method to guarantee its quality.
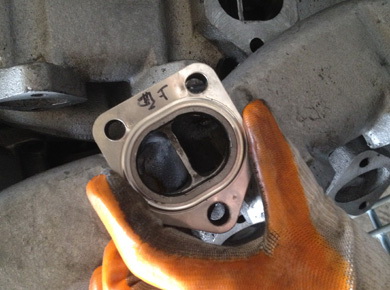
2. Other repairing and inspection works must be performed
accordingly, such as mechanical and chemical inspection, repairing
for small problems and good packing method.
Home |
More Articles |