|
CASTING
I have worked for years in iron and
steel casting area, so always wanted to
write an article to introduce all
aspects for iron and steel casting, and
hope this article could help casting
purchasers to quickly understand all
main issues about castings. Ok, let's
get started!
Casting is a kind of metal part. We need
to melt the iron or steel into hot
liquid, then pour it into pre-made
molds, after cooling, we remove the
molds, then get the iron or steel parts,
we call them as castings. You may
understand some about casting, but start
to wonder what are the molds? Please
keep reading.
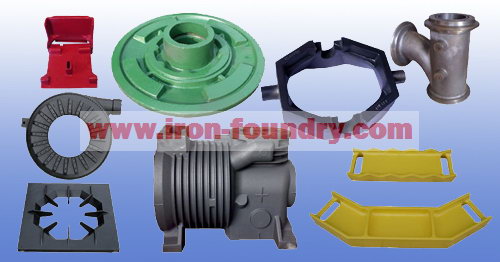
Casting Molds and
Patterns
Many casting buyers may confuse about
the molds and
patterns. Molds usually means
the things we use them to hold the hot
liquid iron during cooling period. There
are many types of molds, such as sand
molds, metal molds, water glass molds,
silica molds etc. Of course, there are
many different types of sand molds, such
as green sand, dry quartz sand, resin
sand, pre-coated resin sand etc. These
molds could resist high temperature, so
they could hold the hot liquid iron.
Then, there is a question now. How can
we make the molds? The answer is the
patterns. We use the patterns to make
the molds. Firstly, we make the patterns
according to the drawings, then use the
patterns to make the sand molds. The
patterns could be made by wood, resin
and metal. Have you understood this
issue? If not yet, please keep reading.
Casting Category
There are many types of castings.
According to the materials, it can be
divided into iron casting, steel
casting, aluminum casting, bronze
casting, brass casting, iron alloy
casting, steel alloy casting, aluminum
zinc alloy casting, plastic casting etc.
Of course, each type can be divided into
many types according to the specific
materials.
According to the
casting processes, casting can
be divided into sand casting, investment
casting, die casting, lost foam casting,
metal mold casting etc. Moreover, sand
casting can be divided into green sand
casting, water glass sand casting, resin
sand casting etc. Want to learn more
about casting processes? You will know
how to do now. Yes, keep reading!
Casting Process
Casting process means the casting
method, by which we produce the
castings. You have known that there are
many types of casting processes, such as
sand casting, investment casting, die
casting, lost foam casting and metal
mold casting. Herein, let's learn more
about these casting processes.
For sand casting process, we use the
sand as the main material for the molds.
In other words, we use the pattern and
mixed sands to make many sand molds,
these sand molds are inside empty, so we
pour liquid iron into the empty
cavities, then liquid iron cool in the
sand molds until become solid parts,
then we break the sand molds, and clean
the surface sands off, then get the
rough castings.
For investment casting process, instead
of sand, we use the water glass or
silica as the main material for the
molds. In other words, we use the metal
patterns and water glass or silica to
form many molds.
For die casting process, we have to use
the die casting machines to inject the
liquid metal into the heat-resistant
metal patterns, then the liquid metal
cool in the metal patterns. Usually, die
casting process can be used to produce
aluminum zinc alloy castings. Not
suitable to produce iron or steel
castings.
For the lost foam casting process, we
need to make a metal pattern, then use
this pattern to make many foam patterns,
then use these foam patterns to make the
sand molds. Then, pour the liquid iron
into the sand molds. The interesting
thing is, we do not take the foam
patterns out from the molds, the foam
patterns will vanish when they meet hot
liquid iron. Lost foam casting process
is not widely used in China, but it is
really suitable to make large metal
castings, and the surface quality is
good.
For metal mold casting process, we need
to make the heat-resistant alloy
pattern, then pour liquid iron or steel
into this pattern directly, and after
cooling, we take the casting out of
metal pattern. Therefore, for metal mold
casting process, the pattern is the
mold. Of course, the surface quality is
good, and less defects, and no sand
residue. However, the alloy pattern is
very costly, and the production rate is
very low.
If you are interested to the above
content, please keep checking the
update. We will complete the following
content and keep updating all content
from time to time.
Casting Characters
Why do the designers choose the casting
process, not forging or welding process?
It is because some special characters of
casting. Casting process can produce
very small and very large metal parts,
and can produce very complex inside and
outside structures. Casting could reduce
the rough weight of metal parts as low
as possible. Lighter rough weight will
mean lower cost for raw materials, and
so for lower costs.
Moreover, there are many types of alloy
cast iron, gray cast iron, ductile cast
iron and vermicular cast iron etc. These
cast irons have different physical
characters, such as abrasive resistance,
high tensile strength, heat resistance
and impact resistance etc. In many
conditions, you could not get these
properties by
forging or
welding process.
Casting Application
Casting is the base of industry. There
are too many areas which need castings.
It is useless to talk about the specific
application. Herein, I just list some
main areas such as automotive industry,
machine tools, stove parts, pipe and
pipe fittings, pumps and valves,
agricultural and engineering machinery,
marine industry. When you see something
made by iron or steel, they are more
likely to be made by casting process.
Casting Products
I used to try to list all casting
products, but I gave up in the end.
There are too many casting products, and
nobody could list all of them. So,
herein, I just list some common casting
products for your reference. For
example,
stove burner, stove plate,
stove grate, stove grill, cast
iron pan,
iron skillet, chimney tube,
stove
door,
bracket, motor case, reducer
shell,
belt pulley,
brake drum,
gear
box,
flywheel, axle support,
cast
iron weight,
pump body,
valve
body,
pipe fitting, manhole and
manhole cover, hand wheel, seal
ring,
flange, wheel hub, frame,
hammer, machine bed, bearing seat,
cylinder block, brake wheel etc.
Casting Main Defects
There are many types of casting defects,
herein, I just list some main common
defects.
1. Sand holes and air holes
Sometimes, it is difficult to
distinguish
sand holes and air holes,
they look like similar defects, just
small holes on the surfaces or inside.
On the surfaces, you could see the few
or many small holes or pits. As for the
inside sand holes and air holes, after
machining, you could see them. As for
the sand holes on the surfaces,
sometimes, they are allowable, but the
for the inside holes, normally
unacceptable.
2. Shrinkage
Shrinkage looks like few very large
irregular holes or many very small
irregular holes. Shrinkage is normally
unacceptable.
3. Crack
As for the steel castings, the crack is
common defect. After machining, crack
will be visible. Since crack will
seriously affect the physical properties
of the castings, so it will be
unacceptable.
These are very common defects, as for
the other defects, you could check our
another article
Common Defects of Iron Castings.
Casting Tolerances
Casting tolerances include two aspects,
one is rough casting tolerance, another
is machining tolerance. As for the rough
casting tolerance, you could refer our
another article
DIN 1686 Standard. As for the
machining tolerance, you could refer
ISO 2768 Standard. These two
standards are commonly used for buyers
and suppliers. However, although
tolerance standards are useful, you
should not take standards as the only
yard for acceptance. Some key dimensions
may need higher tolerance, and if some
dimensions do not affect the use, and
they are difficult to keep, you should
consider to allow looser tolerance.
Casting Prices
All the buyers are caring about casting
prices. The casting prices are mainly
related with the weight of rough
castings, the materials, the
heat treatment, the
complexity of structures, the suited
casting
processes, surface coating and
painting, and the machining costs. The
changes of
casting prices will be mainly
caused by the prices of pig iron or
called materials, and the exchange rate
of currency. For the average prices of
iron and steel castings, you could check
the website of Dandong Foundry. We
update the casting prices there.
Casting Suppliers
As we know, there are four metal casting
manufacturing bases in China. They are
Liaoning, Shandong, Zhejiang and Hebei
provinces. There are also many trading
companies in China, who specializing to
export the metal castings to overseas.
Moreover, there are many machining
workshops who has their own
subcontractors for supplying the rough
castings to them. So, all of them could
be your supplier for
metal
castings in China.
Casting Standards
There are many casting standards, some
for the
tolerances of rough castings,
and some for the
machining tolerance, and some
for the
cast iron grades. These
standards are the useful tools for
buyers and manufacturers.
Casting Machining
Most of castings need some level of
machining, rough machining or finish
machining. Most of
Chinese foundries could do the
rough machining, but only some of them
could do the high-precision finish
machining.
Home |
More Articles |
|