Hard Sand Casting
Hard sand casting means the
sand casting produced by the hard molds, such as
resin sand casting,
shell molding process and
water glass sand casting process.
After hardening process, the sand molds of these
casting processes will
become very hard, so called hard sand casting. A certain intensity
of sand molds will bring many benefits.
1. It will reach high
dimensional tolerance for castings. The hard sand molds will
become hard after hardening process, therefore, they can better
resist the expansion of liquid hot iron, so reach high dimensional
tolerance to CT8 to 10 of standard
ISO 8062.
2. It will keep good
surface smoothness. Resin and water glass mixed with sand
will become smooth after hardening. So, make the surface of sand
molds more smooth than other sand molds.
3. It will reduce casting
defects. There is less sand residues on the surface of hard
sand molds, therefore, will reduce the casting defects such as sand
holes, sand inclusion.
However, hard sand casting processes have some disadvantages too.
1. It will cause higher production costs. Resin material is
expensive, as for the shell molding process, the resin sand can not
be used recycled. So, hard sand casting will be more expensive than
green sand casting
processes.
2. It will reduce the production rate. Compared with other sand
casting process, resin sand casting process has a burning and
hardening process, shell molding needs machines to make the shells
and cores one by one, and water glass sand needs carbon dioxide to
assist hardening. These extra processes will cause lower production
rate than green sand casting processes.
However, these hard sand casting processes are widely used worldwide
because their advantages, and they have remedied the disadvantages
of green sand casting process and other casting processes.

Resin Sand Casting
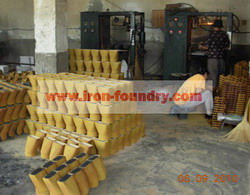
Shell Molding Casting
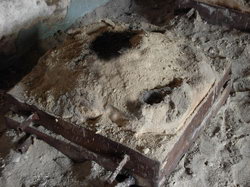
Water Glass Sand Casting
Home |
More Articles |