|
Steel Casting Defects
The mechanical properties of
steel casting are higher
than iron casting, but its
casting character is worse than iron casting. Because of the higher
melting point of steel, the steel liquid is easily oxidized and its
fluidity is very poor, the volume shrinkage rate is 10% to 14% and
the linear shrinkage is 1.8% to 2.5%. In order to prevent missing
portion of casting, cold shut, shrinkage, cracks, sticky sand and
other defects, more complex measures must be taken.
Due to the poor fluidity of liquid steel, the wall thickness of
steel castings can not be less than 8.0 mm in order to prevent cold
shut and missing portion of casting. The structure of the gating
system should be as simple as possible, and the cross-sectional size
is larger than cast iron. Use dry cast type or hot mold and increase
appropriate casting temperature, typically 1520~1600 Celsius degree,
because of the high pouring temperature, overheating degree of
molten steel, and long liquid state, the liquidity can be improved.
But if the gating temperature is too high, it will cause
casting defects
such as coarse grains, thermal cracking, pores and sticky sand.
Therefore, for generally small castings with thin wall and complex
shape, the casting temperature is about steel melting temperature
+150 Celsius degree, while for the large, thick-walled castings, the
pouring temperature is about 100 Celsius degree higher than its
melting point.
Since the shrinkage of steel casting is much larger than iron
casting, in order to prevent shrinkage and other defects, in the
casting process, riser and chiller and subsidies and other measures
are usually taken to achieve progressive solidification.
In addition, to prevent shrinkage, porosity and crack defects, the
wall thickness should be even, avoiding sharp corners and
rectangular structure. Adding sawdust in the foundry sand, adding
coke in the core, and using hollow core and oil sand cores will
improve the yield and permeability of
foundry sand and sand cores.
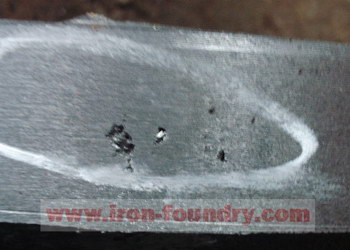
Home |
More Articles |
|