Sand casting and die casting are the main casting production method for aluminum casting products, let us show their difference and compare their advantages and disadvantages.
What is Sand Casting?
In the sand casting production process, molten metal is poured directly from a ladle into a sand mold – no high pressure necessary. The sand mold is created when a pattern made out of metal materials. Following the pour, the metal solidifies, the mold is opened and the sand is shaken off the hot casting, which leads to a product being manufactured. At this point, the gating material can be removed and the casting is complete.
Sand casting process could be used for producing aluminum castings, gray iron, ductile iron castings, and even steel castings.
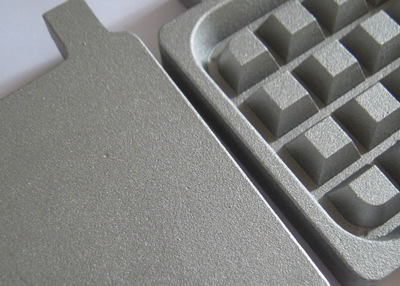
What is Die Casting?
In the die casting production process, liquid or "molten" aluminum is forced into a die under high pressure. In this case, "die" refers to the steel mold (or called as pattern) created to shape the actual product that will be made. Following the pour and injection into the mold, the molten aluminum solidifies and is removed from the mold. When the metal cools, the gating material gets removed and a product has been manufactured! The steel mold can then be closed and prepared for the next "shot," which allows it to be reused immediately. The cycle on making a die cast part can be from 30 seconds to one minute, making the process extremely fast.
However, because the limitation of steel mold, this production process can not be used for producing iron and steel castings, so only can be used for producing aluminum castings.
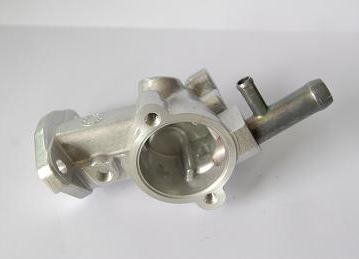 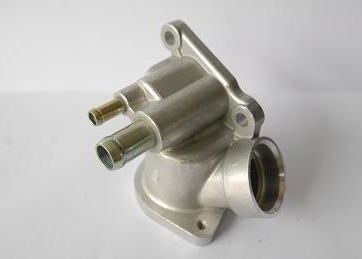
The difference, advantages and disadvantages of sand casting and die casting
1. Sand casting can use iron pattern, aluminum pattern, wooden or plastic patterns, the mold material is sand. Die casting uses alloy steel pattern, also the pattern is the mold too.
2. Sand casting can produce iron, steel, aluminum and brass castings, but die casting can only be used for producing aluminum, zinc, copper and magnesium castings.
3. Sand casting use gravity as the force, die casting uses extra pressure to force the molten metal. So die casting will has higher quality.
4. Die casting can produce more accurate and complex castings, for example, if you will require precision with complex shapes in their castings, die casting most likely makes more sense for their project.
5. Sand casting can be cheaper, for example, a furniture manufacturer may find sand casting to be more cost-effective for their production. Sand-casted parts often come with a thicker wall, so the larger size of the final product can still be accurately produced with less precision. The price will be much cheaper than die castings.
6. The pattern cost (tooling cost) of sand castings is much cheaper than die casting's, one set of die (pattern) for die casting may be 5 to 10 times more expensive than sand casting's.
7. Sand casting process can produce very large castings, but die casting process can only produce small castings, because of their shot machine limitation.
8. The surface and inside quality of die castings are much better than sand castings. Die castings may have crack or pin holes, but sand castings have various defects.
9. The surface quality of the die castings will be much higher and better than sand castings, because the difference of mold material.
How to choose the best production process for your casting products?
Basically, if you want to make aluminum or zinc castings, then you could consider die casting process, for other materials, such as cast iron or cast steel, you can not choose die casting process.
If your demand quantity is low, or tooling cost is limited, then you can not choose die casting process, because of its high pattern cost.
If your casting product is very large, such as larger than 300mm, then you may not be able to find a suitable die casting maker for it.
Therefore, you can consider die casting process basing on the following conditions:
1. The quality requirement is very high.
2. The demand quantity is large enough.
3. The material is aluminum, zinc or copper.
4. The casting size is not too large.
5. You have high budget for unit price and tooling cost.
Otherwise, the sand casting or permanent mold casting process may be the better choice.
|