|
Advantages and disadvantages of shell molding casting
Shell molding casting is a main
sand casting production
process. The castings have good surface smoothness, less
surface defects, and good dimensional accuracy. Our foundry has used
this process for many years.
The followings are the advantages of shell molding castings:
1. Good surface quality
Because shell molding uses phenolic resin as the sand binder, so the
smooth and hard surfaces of sand molds make the castings have good
surface smoothness. The following photo could be taken as sample for
the surface quality.
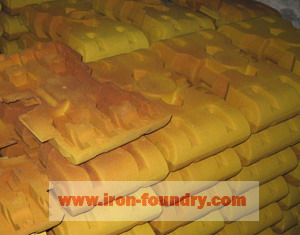
Moreover, this process have less sand
residue during production, so could reduce some
iron casting defects,
such as sand inclusion, sand holes and air holes.
2. High rough casting dimensional accuracy
This molding material is a type of hard mold, so there will be less
swell of sand molds, so the dimensional tolerance will be smaller.
This advantage will be very useful for producing high accuracy rough
castings, and reduce machining cost.
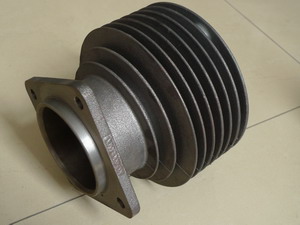
3. Thin wall thickness and complex
castings
Less than 5mm wall thickness will be taken as very thin as for
sand castings. Only shell
molding process could produce these cast products.
In addition, hot shell and core molds are made by molding machines,
so it could produce the castings with complex structures, especially
complex inside structures.
4. Less manpower and molding skill requirements
Since the main works have been completed by the molding machines, so
this process could be operated by women workers, and there is no
special skill required. This is very different with
green sand casting
process.
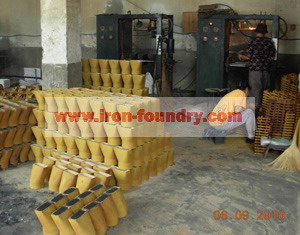
The followings are the disadvantages of
this process.
1. High production costs and casting prices
The phenolic resin sand is more
expensive than green sand and furan resin sand, and it could not be
recyclable. Therefore, shell molding castings will have higher
prices.
2. High pattern costs
This process needs to use
metal patterns
(iron patterns), which will be more costly. So, it is not suitable
for producing small quantity castings and small orders.
3. Size and weight limitation
The shells and cores of castings are produced by shell molding
machines. These machines have dimensional limitation. So, most of
shell molding castings will be less than 400mm length, and less than
20kg weight. Too long or too heavy can not be produced by this
process.
Although shell and core molding process has these disadvantages, but
its advantages are also very important. So, more and more iron
foundries in China are using it to produce small and middle
iron castings. As we know,
in other countries, many metal foundries are using it to produce
steel castings to replace
lost wax casting process.
Home |
More Articles |
|