|
Casting Production - Processes, Costs and Companies
Dandong Foundry has been engaged in
casting production for over 50 years, mainly manufacturing
grey iron,
ductile iron and
cast steel products.
Herein, we will briefly introduce the metal casting production
processes and related costs.
Casting Production Processes
There are many different processes to produce
metal castings. For
examples, sand casting, die
casting, lost wax investment casting, permanent mold casting,
continuous casting, centrifugal casting and vacuum casting etc. As
for sand casting processes,
they could divided into green sand, resin sand, shell molding, water
glass sand, lost foam casting etc.
Each casting process has their own advantages, disadvantages and
production costs, so choosing which production process depends on
the requirements, structural characters and target prices of your
products.
Here are some photos for casting production processes, sand casting
workshops are from Dandong Foundry, others are from the foundries
nearby:
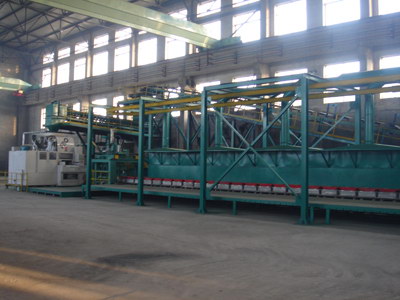
Automatic Molding Production Workshop
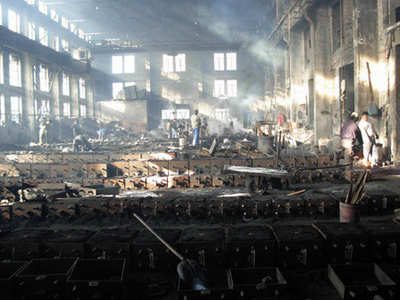
Manual Green Sand Casting Production
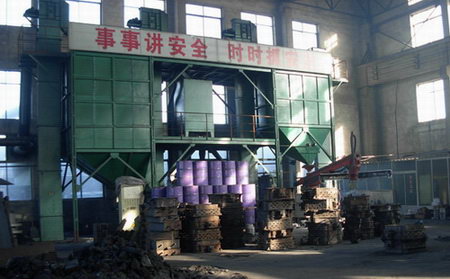
Resin Sand Casting Production Workshop
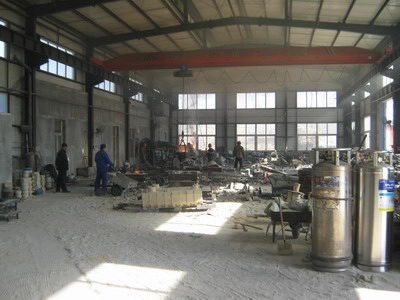
Cast steel 2 Oxygen Sand Molding Production
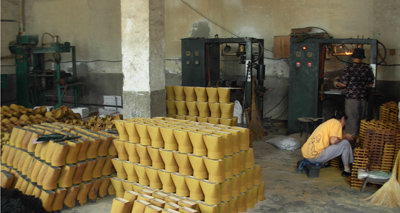
Shell Molding Process
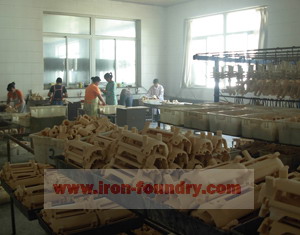
Lost Wax Water Glass Investment Casting Workshop
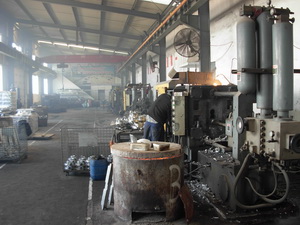
Aluminum and Zinc Die Casting Production Workshop
Casting Production Costs
The casting production costs included several parts.
1. Pig Iron Costs - Pig iron is the main material of iron
castings, so they have taken large part of the total production
costs. For example, if the gray iron casting price is 1.25 USD/kg,
then the pig iron cost will be about 0.59 USD/kg. Therefore, if the
pig iron price is unstable, then it will have big influence to the
casting prices.
2. Labor Costs - In the past, the
labor costs may not be an important part, but after past years, the
labor costs in China have been increased several times, therefore,
they have affected the casting prices clearly now.
3. Coal or Electricity Costs -
The cupola needs foundry coal as the fuel, and medium frequency
furnace needs electricity. Moreover, the heating treatment also
caused the extra electricity costs. These costs are also important
part for the production costs.
4. Alloy and Nodulizer Costs - As
for the high grades of ductile iron and alloy cast metals, the
necessary alloys will be needed to add. As for the ductile iron
materials, the nodulizer (nodulizing agent) will be needed.
5. Extra Sand Costs - As for the
green sand, since they are cheap and recyclable, so their costs will
be small. But as for the resin sand, and shell molding processes,
the sands will be more expensive.
6. Machining Costs - If your
parts need machining works, then you need to consider the machining
costs.
7. Painting and Packing Costs -
There are many types of finish coating, painting, anti-rust oil
protection, and there are several types of packing methods too. All
these costs should be considered.
The final production costs are comprised
by above costs, the different requirements to them will cause the
different casting prices. Please refer to
cast iron and pig iron prices for the latest prices.
Casting Production Companies
There are thousands of metal casting production companies in China,
so we call them as iron
foundries, steel foundries,
aluminum foundries, copper foundries etc. Larger foundries may be
able to produce two types of casting materials, but no company could
produce all types of materials. It is because different materials
will need different casting processes and equipments.
Casting Production International
Casting production is a high pollution and high energy consumption
industry. So, most of
metal foundries are located in China and India. Of course,
China government is closing the small foundries and controlling the
pollution and energy consumption by some policies. But the export
volume of metal castings from China is still very large.
Most of large metal casting manufacturers could understand the
international standards and requirements, and have their own
exporting licenses.
Home |
More Articles |
|