|
No Bake Sand Casting
The Molding Process:
No Bake is a casting process that uses chemical binders to bond the
molding sand. The sand is then transported to the mold fill station
in preparation for filling of the mold. A mixer is then used to
blend sand with the chemical binder and the catalyst. When the sand
exits the mixer, the binder begins the hardening process.
After the compaction process, a rollover process is used to remove
the mold from the pattern box. The mould is then readied for
handling the molten metal. After a shakeout process, the molded sand
is taken away from the casting. Then various procedures follow
including the finishing and the sand can be reclaimed by thermal
means.
In the No-Bake
resin sand casting process, sand molds are created using
a wood, metal, or plastic pattern. Sand is mixed with a plastic
binder in a high-speed mixer. This sand is deposited into box
containing the pattern and all essential gating, risers and chills
for pouring.
The sand mixture sets up hard in a few minutes and the mold is
removed from the pattern. Cores for forming internal passages in the
castings are made using the same process. Cores are carefully placed
into the molds. The molds are then closed and are ready for pouring.
The chemical nature of the binders makes this a highly specialized
process that has to been handled with considerable expertise and
knowledge.
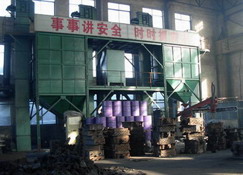
Features:
The No-Bake casting technique creates molds with excellent
dimensional stability. The casting surface finish is also improved
over other sand casting processes. No-Bake is one of the most
efficient and advanced sand casting techniques currently available.
No-Bake Sand Molding requires a chemical binder to hold the sand
together. This type of system allows for the production of more
complicated castings. Castings that are selected for this process
usually are extremely large castings, require deep pockets, or
limited draft situations.
Another important feature to No-Bake Sand Molding is that there are
no products of combustion incorporated in the material.
Consequently, castings that require a high level of x-ray quality
can be produced on a regular basis.
So, the chemical binders are used to create high strength moulds.
When the temperature is brought to normal levels, the molds turn
rigid.
Advantages:
1. It is adaptable to any quality.
2. It creates high strength moulds and improves dimensional
repeatability.
3. Requires low skill and labor requirements
4. Provides better dimensional control.
Home |
More Articles |
|