|
The difference of gray iron and ductile iron
castings
The followings are the main difference and
properties of gray iron castings
and ductile iron castings.
Gray iron is selected for ease of machining, high compressive
strength, better thermal conductivity and excellent vibration
absorption.
Carbon content is by far the most important element for gray iron
(usually 2% to 4%) to create tensile strength and machinability.
When molten cast iron solidifies some of the carbon precipitates as
graphite, forming tiny, irregular flakes within the crystal
structure of the metal which enhances the desirable properties of
cast iron, the flakes disrupt the crystal structure leading to cast
iron's characteristic brittleness.
Mechanical
Properties |
Class 25 |
Class 30 |
Class 35 |
Class 40 |
Class 45 |
Class 50 |
Tensile Strength (PSI) |
25,000 |
30,000 |
35,000 |
40,000 |
45,000 |
50,000 |
BHN (Typical) |
150-241 |
170-241 |
187-241 |
187-255 |
196-255 |
196-269 |
Suggested Min.
Wall Thickness |
3/16" |
3/16" |
3/8" |
1/2" |
5/8" |
3/4" |
So, the gray iron is suitable material
to produce iron casting parts of machine base, counter weights,
stove parts, boiler parts, pump shells etc.
In ductile iron the graphite forms into
spherical nodules rather than flakes, thus inhibiting the creation
of cracks and providing the enhanced ductility that gives the alloy
its name. Ductile iron has higher tensile strength and toughness
similar to steel.
Mechanical
Properties |
60-40-18 |
65-45-12 |
80-55-06 |
100-70-03 |
Tensile Strength
(Min PSI) |
60,000 |
65,000 |
80,000 |
100,000 |
Yield Strength (Min
PSI) |
40,000 |
45,000 |
55,000 |
70,000 |
Minimum Elongation
in 2" |
18% |
12% |
6% |
3% |
BHN (Typical) |
143-187 |
156-217 |
187-255 |
240-302 |
So, ductile iron has wider application
fields than gray iron. It could be used to produce casting parts for
truck, tractors, machinery parts, auto parts etc.
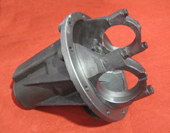 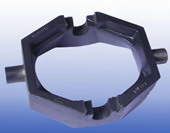 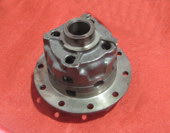
Home |
More Articles |
|