|
Electrophoretic paint for iron casting parts
Electrophoretic paint is also known as
cataphoresis painting, KTL painting or electrophoretic coating,
which is a new type of paint with low pollution, energy saving,
resource saving and good anti corrosion. Currently, electrophoretic
paint is widely used to iron
casting parts for automotive, mechanical, and home
appliances.
Types of electrophoretic paint
There are two types of electrophoretic paint, one is anodic
electrophoresis paint (ED), another is cathodic electrophoretic
paint.
Anodic electrophoresis paint is using carboxylate with high acid
value to form a potential difference at the two poles. So, there is
Electronic precipitation at the anodized surfaces. The positive pole
is the iron casting part, so the
paint will be covered on its surfaces.
Cathodic electrophoretic paint is using a cation type compounds,
after dissolution, they could form potential difference at the two
poles, so there is electronic precipitation at the surfaces of
cathode surfaces.
Characters of electrophoretic coating
1. Electro Deposition can achieve fully automatic production, so
will increase productivity, therefore, it is more suitable for the
large volume flow production.
2. ED has high swimming through rate, and low viscosity, so easier
to reach the groove shape positions and cracks. Especially suitable
for iron casting parts, because its high electrical conductivity.
3. The utilization rate of the paints could reach 95% to 100%, so
this process could save materials, and so reduce the painting costs.
4. Electrophoretic paint has good anti-rust ability because of its
uniform thickness of coating, and good adhesive force.
5. Electrophoretic paint demand less solvent, so it is better for
environmental protection, and higher safety for production.
The advantages compared with electroplate, spray
paint and dipping paint
1. Compared with spray painting and dipping paint, the
electrophoretic paint can control the thickness of coating more
easier and accurate.
2. As for the iron castings with complex inside structures, the ED
could form uniform coating.
3. The ED has low moisture content, so the thickness is uniform, and
free of ripple and nodule problems.
4. Electrophoretic paint does not use organic solvent, so will not
cause fire disaster or heavy metal poisoning, and pollution
problems.
The disadvantages of ED
1. The ED requires the electrical conductivity of coated parts, so
it is more suitable for metal parts,
such as iron and steel castings
parts.
2. The coating of cathode electrophoresis paint has higher anti-rust
capability, but it is hard and brittle, not very flexile, and worse
glossiness. So, it is more suitable for primer painting.
3. The coating of anodic electrophoresis paint has better
glossiness, anti ultraviolet radiation resistant aging, better
appearance, so suitable for finish coating, but it is has worse heat
resistance and abrasive resistance.
In China, most of iron
foundries can not perform this coating in-house, but there
are some professional coating workshops providing this service. So,
iron foundres could entrust them to do the electrophoretic paint for
their cast iron and cast steel products.
As for the costs of KTL painting, it is not cheap. It is more costly
than electroplating,
and almost same price with the hot dip galvanizing.
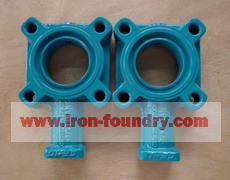 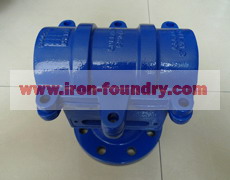
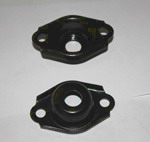 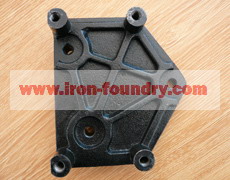 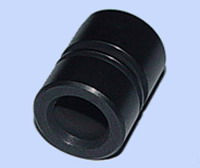
Home |
More Articles |
|