|
The difference between green sand casting process and resin sand
casting process
In the past, one client asked us the
difference between green sand casting process and resin sand casting
process. Herein, I make a brief introduction to these two casting
processes, and hope it could be helpful for other casting
purchasers.
Green sand casting process is screening and mixing the wet sands,
and filling the sands into the sand boxes, then use machines or just
by workers to tamp the sands, then pouring the liquid iron into the
sand molds.
Resin sand casting process is mixing the furan resin and sand
together, then filling the mixed sands into the sand boxes, then
after tamping, using the paints to flush the surfaces of molds, then
burning the paints to make the sand molds to become very hard,
finally, pouring the liquid iron into the solid sand molds.
1. Materials
The green sand casting process mainly uses the green sands as the
molding material. The green sand is a kind of wet sand.
The resin sand casting process mainly uses the resin sand as the
molding material, and need to use the alcohol paints.
Since the furan resin is more expensive, the resin sand castings
will be more expensive than green sand castings.
2. Equipments
As for the traditional green sand casting process, it only needs
sand boxes and workers, so no equipment needed. Today, more and more
iron foundries in China use
molding machines or automatic
molding machines.
The resin sand casting process usually needs equipments to mix the
resin sand and fill the sands into the sand boxes.
3. Production time
The resin sand casting process has an extra time to flush the
paints, and burn the paints and wait the resin molds become hard.
Therefore, it needs more production time, therefore, more costs.
If the green sand casting process uses
the automatic molding machines, it will have very high production
rate, one FBO molding line
could normally produce 20 tons each day. Therefore, automatic
molding line usually produce iron castings
for the automotive industrial.
4. Casting quality
The casting quality has big difference for these two processes.
Since resin sand casting process uses the hard molds, therefore,
resin sand castings have better surface smoothness, higher
dimensional tolerance, and less surface and inside
casting defects, such
as sand holes, air holes and shrinkage.
4. Suitable casting products
Resin sand casting process is suitable to produce large iron
castings with weight range from dozens of kilograms to several tons.
Green sand casting process is suitable to produce small and medium
castings with weight under 50 kilograms. Interestingly, as for the
very large iron castings with weight of several tons, such as the
dryer cylinders for the paper manufacturing machinery, the green
sand casting process is the suitable choice. However, you can not
produce so large castings by sand boxes, but just produce them by
digging the large holes under ground.
Although there are so many differences between these two casting
processes, it is not absolutely to judge your parts have to use
certain casting process, the iron foundries should consider the
suitable production process according to their technical conditions
and capability.
The following photos are the green sand
and resin sand casting workshops in
Dandong Foundry in
China.
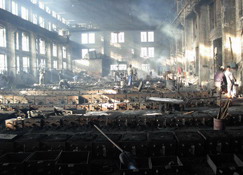
Green Sand Casting Workshop
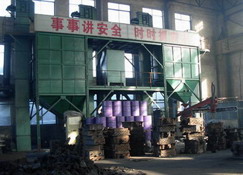
Resin Sand Casting Workshop
Home |
More Articles |
|