Cast Iron in Ancient China
This article is a revised version of a
talk Mr. Donald B. Wagner gave at the one-day Symposium on Cast Iron
in Ancient China. We listed some main part of content to share with
the friends working in iron casting industry.
We can see that casting steel, with up to about 1.5% carbon,
requires temperatures well over 1500 centigrade. Such temperatures
were often reached in early times in various parts of the world, but
the refractory materials necessary to manipulate molten steel and
cast it into useful artifacts were not developed until the late 19th
century, in Britain.
With a higher carbon content, 3 - 4%, practical casting is much
easier, requiring temperatures around 1300 centigrade. Iron with
this carbon content is called "cast iron" because it is easy to form
by casting. It lends itself well to large-scale production, which
has always been important in ancient China. It was undoubtedly the
use of cast iron in ancient China that made it possible for every
peasant to have iron implements.
White Cast Iron
The use of cast iron makes it possible to mass-produce implements
cheaply, but for most implement types it has inferior mechanical
properties. All pre-modern Chinese cast iron has a very low silicon
content, usually under 0.5% Si, and therefore solidifies as "white
cast iron", in which the carbon is present as cementite, Fe3C, which
is extremely hard, harder than quartz, and this makes the iron
brittle.
An example is this mattock-head. The micrograph shows that it is
white cast iron. Its hardness may be an advantage with such an
implement, for it would be very abrasion-resistant. But the worker
would have had to be careful, for if it hit a rock it might shatter.
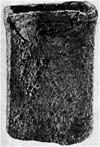 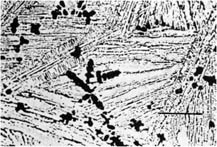
Coins were usually made of copper
alloys, but sometimes shortages of copper made it necessary to cast
them of iron. Here are three iron coins, from the Western Han, Song,
and Qing periods.
  
Mike Wayman and Helen Wang studied 37
iron coins of the Song period in the British Museum, London. They
are all of white cast iron, and their article has a great deal of
detail on the types of white cast iron found here.
An interesting aspect is revealed by X-rays of some of the coins:
these show that there are sometimes quite large casting bubbles in
the coins, making them feel distinctly light in the hand. It seems
possible that the coin-founders intended these bubbles, in order to
save material.
This is a cast-iron mirror – probably Han-dynasty (206 BC – AD 220),
probably white cast iron.
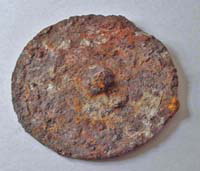
An interesting characteristic of
traditional Chinese metallurgy is that cast iron is often combined
with other materials. The legs of this vessel are cast iron, while
the body is bronze. I have not seen a metallurgical investigation of
a vessel of this type, but the legs are most probably of white cast
iron.
The vessel is a Ding from a grave excavated at Yutaishan in
Jiangling, Hubei, dated to the 4th century BC.
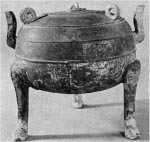
Malleable Cast Iron
These crossbow-bolts have bronze tips and iron shafts – presumably
because bronze has better casting properties than iron, while iron
is cheaper than bronze.
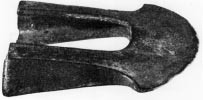
Lian Haiping in Shanghai has studied
some examples of this type of artefact and found that the shafts are
of cast iron which has been decarburized in the solid state – this
type of iron is called “whiteheart malleable cast iron”. She
reported this at the BUMA conference in Beijing in 2006.
This implement-cap is “blackheart malleable cast iron” – it was
first cast, then annealed at a high temperature, probably around
950°C, for a period of days. This treatment caused the carbon in the
iron to precipitate as graphite, making a material which has much
better mechanical properties than ordinary cast iron (white or
grey).
These gads from a copper-mine site show how tough the ancient
Chinese cast iron could be. They are obviously subject to very hard
punishment, being hammered into cracks in the rock.
But they are of cast iron – again annealed at a high temperature for
a period of days, this time decarburizing the iron at the surface
and precipitating graphite farther in.
These scissors are also of cast iron. They were cast, then annealed
in an oxidizing atmosphere to decarburize to a uniform carbon
content around 1%, with a few very small grapite nodules, then bent
into shape by a smith.
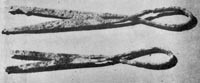
Grey Cast Iron
That in itself is surprising enough, but note that the iron is very
low in both carbon and silicon, and nevertheless the structure is
grey cast iron.
Normally such an alloy would solidify as white cast iron – only very
slow cooling would allow it to solidify as grey cast iron.
This must have been cast in a massive heated ceramic mould and
allowed to cool very slowly, over a period of days.
The only ancient artefacts I know of which are grey-cast are moulds,
and I believe the reason is that the moulds must be very tough, to
tolerate the thermal shock when molten iron is poured in, but they
could not be made of malleable cast iron, because the annealing
process tends to warp castings slightly, so that it would be
difficult to fit the parts of the mould together.
More Uses for Cast Iron in China
Cast Iron Woks
Here is a wok – that is the usual English word, which comes from the
Cantonese pronunciation, which in Mandarin is pronounced huo. It is
broken, so it was possible to measure the thickness at its thinnest
part.
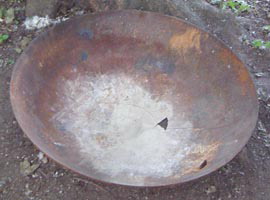
How they were cast in the 19th century
can be seen here. They are still being cast today, probably by
different methods. It is interesting to note that cast-iron woks are
now being imported to Europe in large numbers and used as portable
fireplaces.
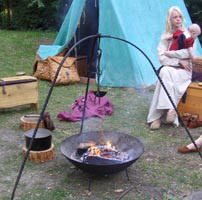
Monumental Castings
Another major use for cast iron was for statues and other large
monuments. This is a quite famous cast iron statue, one of four at
the Zhongyue Temple in Dengfeng, cast in AD 1024.
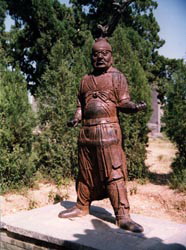
By studying the mould-seams on statues
like this one and the next we can learn a lot about how these
statues were cast.
In this case we have a very interesting phenomenon. The photograph
shows what looks like a repair to the statue, but in fact it
represents a repair to the mould.
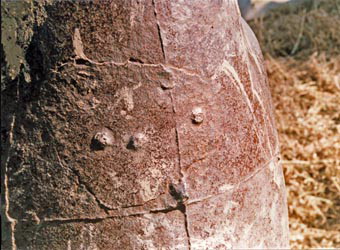
Something happened to the mould – it
broke and had to be repaired. The bumps which can be seen are
probably the heads of spikes that were used to hold the repair in
place.
Cast Iron Bells
I think it is only in China that bells have been made of cast iron.
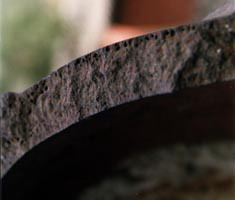
This broken bell is interesting because
we can see in the fracture that something has gone wrong. Those air
bubbles at the surface would (I believe) have had a bad effect on
the tone of the bell.
Probably the founders added sulphur to the iron to assure that it
would solidify as white cast iron, but added too much, so that the
bubbles formed.
Cast Iron Cannons
The ancient founders' experience in casting statues and such came in
very handy when they began casting iron cannons. The first iron
cannons in China come at the very beginning of the Ming Dynasty, in
the 1370's.
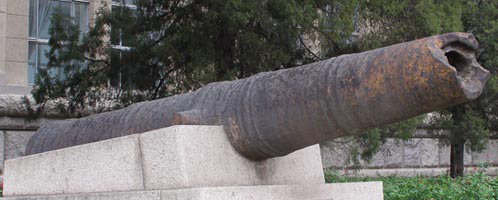
The cannon above is probably a
combination of materials – wrought iron and cast iron – as we can
see at the right: two cannons with wrought iron inside and cast iron
outside. George Banks sketched these at the Dagu Forts, in modern
Tianjin, in 1860. He believed that these were 'evidently very old',
from the +17th century or before; while this dating is quite
plausible it is not clear what evidence he could have had for it. He
does not mention any inscriptions.
Home |
More Articles |